In the dynamic world of industrial applications, the demand for efficient and reliable fluid control systems is ever-increasing. Among the innovations that have emerged to meet this demand are composite push to connect fittings. These fittings are not just a trend; they represent a significant advancement in the way we manage fluid systems, combining lightweight materials with robust performance. This article delves deep into the characteristics, benefits, applications, and installation of composite push to connect fittings, providing you with all the information you need to make informed decisions for your fluid control needs.
What Are Composite Push to Connect Fittings?
Composite push to connect fittings are specialized connectors designed to facilitate quick and secure connections in pneumatic and fluid systems. Unlike traditional fittings made from metals or rigid plastics, composite fittings utilize advanced materials that blend strength, flexibility, and resistance to environmental factors. The composite materials often include a combination of polymers reinforced with fibers, which enhances their durability and performance.
How Do They Work?
The operation of composite push to connect fittings is straightforward yet effective. The fittings feature a unique mechanism that allows for rapid installation without the need for tools. When you insert the tubing into the fitting, a series of internal components, including a gripping mechanism and a sealing element, engage with the tubing. This design creates a secure, leak-proof connection that can withstand varying pressures and temperatures. The push-to-connect feature not only simplifies the installation process but also allows for easy disconnection and reconnection, making maintenance and adjustments hassle-free.
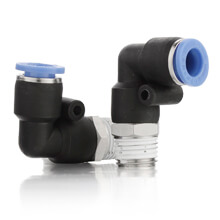
What Are the Benefits of Using Composite Push to Connect Fittings?
- Lightweight Design: One of the most significant advantages of composite fittings is their lightweight nature. This characteristic reduces the overall weight of the fluid system, which is particularly beneficial in applications where mobility is essential, such as in robotics or portable equipment.
- Corrosion Resistance: Composite materials are inherently resistant to corrosion and chemical degradation. This property makes them ideal for use in environments where exposure to harsh chemicals or moisture is a concern, ensuring longevity and reliability.
- Enhanced Durability: Composite fittings are engineered to withstand high pressures and temperatures, making them suitable for demanding applications. Their robust construction minimizes the risk of failure, which can lead to costly downtime and repairs.
- Cost-Effectiveness: While the initial cost of composite fittings may be higher than traditional options, their durability and reduced maintenance needs lead to long-term savings. Fewer replacements and repairs translate to lower operational costs over time.
- Versatility: These fittings can be used with a variety of tubing materials, including polyurethane (PU), nylon, and polytetrafluoroethylene (PTFE). This versatility allows for greater flexibility in system design and application.
In What Applications Are Composite Push to Connect Fittings Commonly Used?
Composite push to connect fittings are utilized across a wide range of industries due to their adaptability and performance. Here are some key applications:
- Automotive Industry: In automotive manufacturing, these fittings are used in air brake systems and pneumatic tools, where reliable connections are crucial for safety and efficiency. Their ability to withstand vibrations and pressure fluctuations makes them ideal for this environment.
- Manufacturing and Automation: In automated assembly lines, composite fittings facilitate quick changes and repairs, minimizing downtime. Their ease of installation allows for rapid adjustments to production lines, enhancing overall productivity.
- Food and Beverage Processing: The food industry demands high standards of hygiene and safety. Composite fittings, with their resistance to chemicals and ease of cleaning, are perfect for applications in food and beverage processing, ensuring compliance with health regulations.
- Medical Equipment: In medical applications, where precision and reliability are paramount, composite fittings are used in various devices and systems, including respiratory equipment and fluid delivery systems.

How to Select the Right Composite Push to Connect Fittings?
Selecting the appropriate composite push to connect fittings involves several critical considerations:
- Application Requirements: Assess the specific needs of your system, including the type of fluid being transported, the operating pressure, and the temperature range. Understanding these parameters will guide you in choosing the right fitting.
- Fitting Type: Determine the type of fitting that best suits your installation. Options include straight, elbow, and tee fittings, each serving different purposes in fluid routing.
- Material Compatibility: Ensure that the fitting material is compatible with the fluids being transported. For instance, if you are working with aggressive chemicals, select fittings made from materials that can withstand such exposure.
- Pressure and Temperature Ratings: Check the pressure and temperature ratings of the fittings to ensure they can handle the maximum operating conditions of your system. This information is typically provided by the manufacturer.
- Installation Environment: Consider the environment in which the fittings will be used. If they will be exposed to extreme temperatures or corrosive substances, ensure that the selected fittings are designed to withstand those conditions.
What Are the Installation and Maintenance Considerations?
Installing composite push to connect fittings is a straightforward process that can be completed quickly. Here’s a step-by-step guide:
- Prepare the Tubing: Cut the tubing to the desired length using a clean, straight cut. Ensure that the cut is perpendicular to the tubing to facilitate a proper seal.
- Insert the Tubing: Push the tubing into the fitting until it reaches the internal stop. You should feel a slight resistance as the gripping mechanism engages.
- Check for Leaks: After installation, it’s essential to test the connection under pressure to ensure there are no leaks. If you notice any leaks, remove the tubing and reinsert it, ensuring it is fully seated.
Maintenance Tips
- Regular Inspections: Periodically inspect the fittings for signs of wear, damage, or corrosion. Early detection of issues can prevent system failures.
- Cleaning: Keep the fittings clean, especially in food and beverage applications. Use appropriate cleaning agents that are compatible with the fitting materials.
- Replacement: If you notice any signs of damage or degradation, replace the fittings promptly to maintain system integrity.
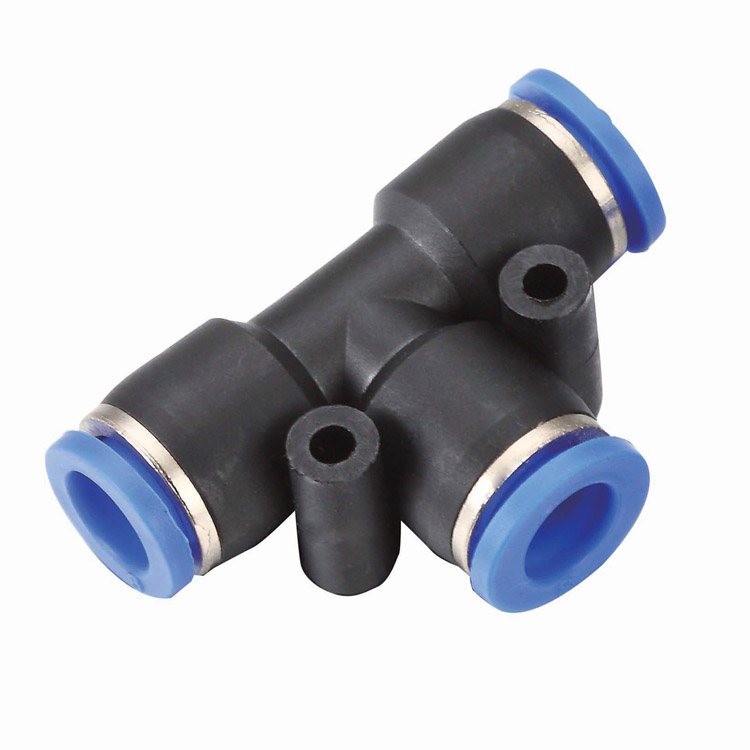
Industry Insights: Common Troubleshooting Tips for Composite Push to Connect Fittings
Even the best fittings can encounter issues. Here are some common problems and their solutions:
- Leaks: If you experience leaks, first check that the tubing is properly inserted. If the fitting is damaged or worn, it may need to be replaced.
- Pressure Drops: A significant drop in pressure may indicate a blockage or a faulty fitting. Inspect the system for obstructions and replace any compromised fittings.
- Difficulty in Disconnection: If you find it challenging to disconnect the tubing, ensure that you are using the correct technique. Most fittings have a release mechanism that should be engaged to allow for easy disconnection.
With over 20 years of experience in the industry, I’ve seen firsthand how proper selection and maintenance of fittings can significantly impact system performance.
Conclusion
Composite push to connect fittings are revolutionizing fluid control technology, offering a blend of lightweight design, durability, and cost-effectiveness. By understanding their benefits, applications, and installation processes, you can enhance the efficiency and reliability of your fluid systems.