Air fittings are critical components in pneumatic systems, serving as the connectors that facilitate the transfer of compressed air between hoses, tools, and equipment. Understanding air fittings is essential for anyone involved in the operation, maintenance, or design of pneumatic systems, whether in industrial settings, automotive repair, or DIY projects. The right air fittings not only ensure efficient operation but also enhance safety and reliability. In this comprehensive guide, I will explore the various types of air fittings, their materials, how to choose the right ones, and best practices for installation and maintenance.
What Are Air Fittings?
Definition and Purpose
Air fittings are specialized connectors designed to join hoses and tools in pneumatic systems. Their primary purpose is to create secure, leak-proof connections that can withstand the pressures and demands of various applications. By facilitating the transfer of compressed air, air fittings enable tools and equipment to function effectively, making them indispensable in a wide range of industries.
Importance of Air Fittings
The significance of air fittings cannot be overstated. They play a vital role in ensuring that pneumatic systems operate efficiently and safely. A well-designed fitting prevents air leaks, which can lead to decreased pressure, inefficient tool operation, and increased energy consumption. Additionally, properly maintained fittings contribute to the overall safety of pneumatic systems by minimizing the risk of accidents caused by air loss.
Types of Air Fittings
Understanding the different types of air fittings is crucial for selecting the right components for your specific needs. Here’s a detailed look at the most common types of air fittings:
1. Push to Connect Fittings
Description: Push to connect fittings, also known as push-in fittings, are designed for quick and easy connections. The mechanism is straightforward: you push the hose into the fitting, and it locks in place, creating a secure seal.
Advantages:
- Ease of Use: No tools are required for installation, making them ideal for quick changes.
- Versatility: Compatible with various tubing materials, including polyurethane (PU), nylon, and polyethylene (PE).
- Leak Prevention: The internal mechanism ensures a tight fit, minimizing the risk of leaks.
Common Applications: These fittings are widely used in manufacturing environments, automotive repair shops, and home workshops where frequent disconnections are necessary.
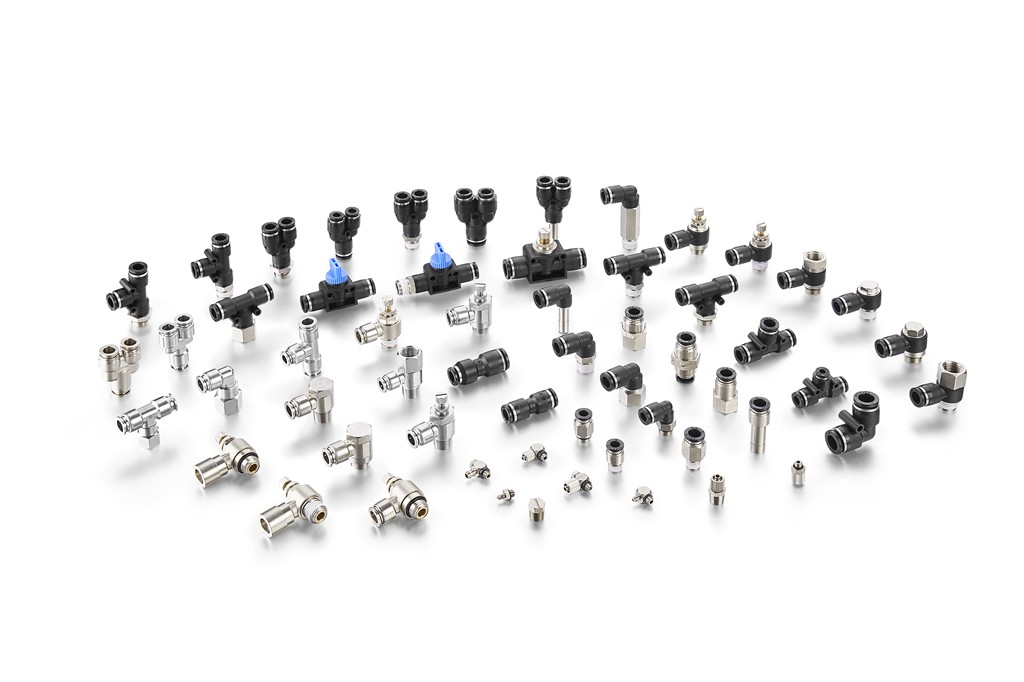
2. Barbed Fittings
Description: Barbed fittings feature a series of ridges or “barbs” that grip the tubing when it is pushed onto the fitting. This design creates a tight seal, making barbed fittings suitable for low-pressure applications.
Advantages:
- Cost-Effective: Generally less expensive than other fitting types.
- Secure Connection: The barbs provide a strong grip on the tubing.
Common Applications: Barbed fittings are often used in irrigation systems, low-pressure air applications, and situations where a permanent connection is desired.

3. Threaded Fittings
Description: Threaded fittings consist of male and female threads that screw together. They provide a robust and leak-proof connection, making them suitable for high-pressure applications.
Advantages:
- Durability: Threaded connections are strong and reliable.
- Versatility: Can be used in a wide range of applications, including high-pressure systems.
Common Applications: These fittings are commonly used in industrial applications, hydraulic systems, and any situation where high pressure is involved.

4. Quick Coupler Fittings
Description: Quick coupler fittings allow for rapid connection and disconnection of hoses and tools. They are designed for ease of use, enabling you to connect and disconnect with one hand.
Advantages:
- Speed: Ideal for environments where tools need to be swapped frequently.
- Convenience: Easy to use, even in tight spaces.
Common Applications: Quick couplers are widely used in automotive repair shops and construction sites where multiple tools are used.
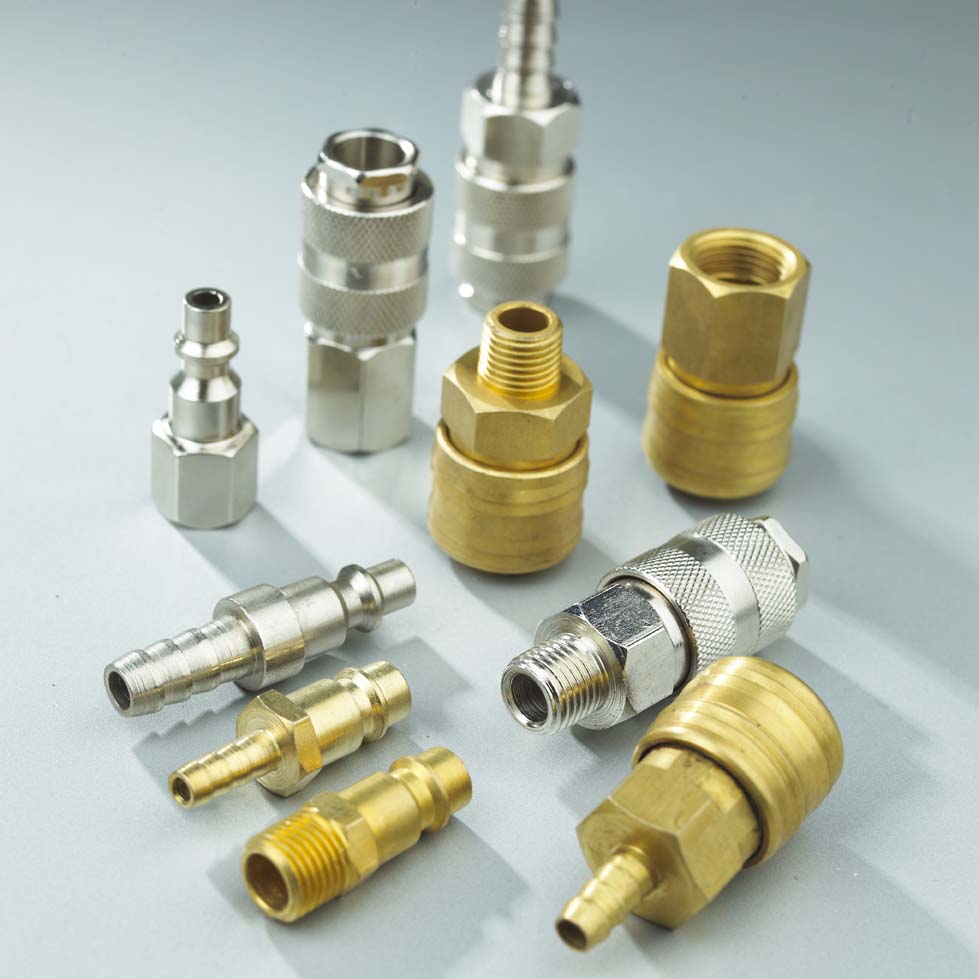
5. Compression Fittings
Description: Compression fittings use a compression ring to create a tight seal between the fitting and the tubing. They are often used in applications where a secure connection is critical.
Advantages:
- Strong Seal: Provides a reliable and leak-proof connection.
- Versatile: Can be used with various tubing materials.
Common Applications: These fittings are commonly found in plumbing and HVAC systems, as well as applications requiring high-pressure connections.

6. Flare Fittings
Description: Flare fittings feature a conical shape that allows for a tight seal when two flared surfaces are joined together. They are commonly used in high-pressure applications.
Advantages:
- High Pressure: Suitable for high-pressure systems due to their robust design.
- Durability: Resistant to vibration and thermal expansion.
Common Applications: Flare fittings are often used in refrigeration and air conditioning systems, as well as automotive fuel lines.
7. Push-On Fittings
Description: Push-on fittings are designed for quick connections without the need for clamps or tools. They are typically used with soft tubing materials.
Advantages:
- Quick Installation: Easy to install and remove.
- No Tools Required: Ideal for temporary connections.
Common Applications: These fittings are commonly used for air and fluid transfer in low-pressure applications, as well as in DIY projects and home workshops.
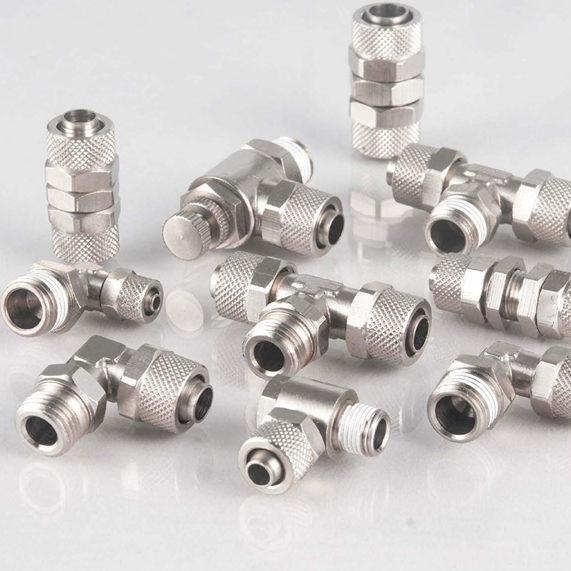
8. Hose Barb Fittings
Description: Hose barb fittings have a tapered end that allows for easy insertion into hoses. They are designed to create a secure connection through friction.
Advantages:
- Simple Design: Easy to use and install.
- Cost-Effective: Generally inexpensive and widely available.
Common Applications: Hose barb fittings are often used for low-pressure air and fluid transfer, including garden hoses and irrigation systems.
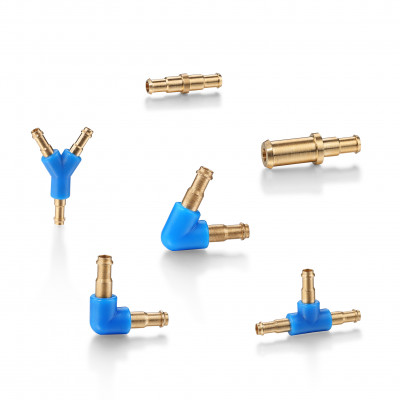
Materials Used in Air Fittings
What Materials Are Commonly Used for Air Fittings?
The materials used in air fittings significantly affect their performance and durability. Common materials include:
- Brass: Known for its strength and resistance to corrosion, brass fittings are ideal for high-pressure applications.
- Stainless Steel: Offers excellent durability and resistance to rust, making it suitable for harsh environments.
- Plastic: Lightweight and cost-effective, plastic fittings are often used in low-pressure applications and for temporary connections.
Choosing the right material is essential for ensuring that the fittings can withstand the specific conditions of your application.
How to Choose the Right Air Fitting
What Factors Should You Consider When Selecting Air Fittings?
When selecting air fittings, consider the following factors:
- Pressure Ratings: Ensure that the fittings can handle the pressure requirements of your system. Using fittings with inadequate pressure ratings can lead to failures and safety hazards.
- Compatibility: Match the fittings with the hoses and tools you are using to ensure a secure connection. This includes checking the fitting size and connection method.
- Application Requirements: Consider the specific needs of your application, such as temperature, chemical exposure, and frequency of use. Different materials and designs may be better suited for specific environments.
Taking these factors into account will help you choose the right fittings for optimal performance.
Installation and Maintenance of Air Fittings
How to Properly Install Air Fittings?
Proper installation is crucial for ensuring leak-free connections. Here’s a step-by-step guide:
- Prepare the Fitting and Hose: Ensure both the fitting and hose are clean and free from debris. A clean connection surface is essential for a secure seal.
- Insert the Hose: For push to connect fittings, simply push the hose into the fitting until it clicks. For barbed fittings, slide the hose onto the barb until it reaches the base. For threaded fittings, apply Teflon tape to the threads before screwing them together.
- Secure the Connection: For threaded fittings, screw them together tightly, but avoid overtightening, which can damage the threads. For compression fittings, tighten the compression nut to create a secure seal.
- Test for Leaks: Once installed, turn on the air supply and check for leaks. If you notice any escaping air, recheck the connections and ensure everything is properly seated.
What Maintenance Is Required for Air Fittings?
Regular maintenance is essential for prolonging the life of air fittings. Here are some best practices:
- Inspect Regularly: Periodically check fittings for signs of wear, corrosion, or damage. Replace any fittings that show signs of deterioration to prevent leaks and failures.
- Clean Fittings: Keep fittings clean and free from debris. Use a soft cloth to wipe down fittings and remove any dirt or grime that may affect their performance.
- Replace as Needed: If you notice any leaks or performance issues, replace the fitting immediately to avoid further complications. It’s better to address small issues before they escalate into larger problems.
Common Issues with Air Fittings
What Are the Most Common Problems with Air Fittings?
Common issues with air fittings include:
- Leaks: Often caused by improper installation or worn fittings. Regular inspection can help identify leaks early.
- Wear and Tear: Over time, fittings can become damaged due to exposure to pressure, temperature, and chemicals.
- Compatibility Problems: Using the wrong type of fitting can lead to connection failures. Always ensure compatibility with hoses and tools.
Troubleshooting Tips
If you encounter issues with your air fittings, consider the following troubleshooting tips:
- Identify the Source of Leaks: Use soapy water to check for bubbles at connection points, indicating leaks. This method is effective for pinpointing the exact location of a leak.
- Recheck Connections: Ensure all fittings are properly seated and tightened. Sometimes, a simple adjustment can resolve the issue.
- Consult Manufacturer Specifications: If unsure about compatibility or installation, refer to the manufacturer’s guidelines for the best practices.
Conclusion
Understanding air fittings is essential for anyone working with pneumatic systems. By recognizing the different types of fittings, their materials, and how to choose and maintain them, you can ensure optimal performance and safety in your applications. Whether you’re in an industrial setting, an automotive shop, or working on DIY projects, selecting the right air fittings will enhance the efficiency and reliability of your pneumatic system.