Pneumatic systems are a fundamental aspect of modern industrial applications, utilizing compressed air to perform a wide range of tasks. Understanding whether pneumatic systems are classified as mechanical or electrical is crucial for anyone involved in engineering, manufacturing, or maintenance. This classification not only affects how these systems are designed and implemented but also influences their efficiency, reliability, and suitability for specific applications. In this article, I will provide a comprehensive overview of pneumatic systems, clarify their classification, and discuss the implications of this classification in various industrial contexts.
What Are Pneumatic Systems?
Pneumatic systems are systems that use compressed air to transmit and control energy. They consist of several key components:
- Air Compressors: These devices convert electrical energy into potential energy stored in compressed air. The compressor draws in ambient air, compresses it, and stores it in a tank for later use. The efficiency of the compressor is critical, as it determines how quickly and effectively air can be supplied to the system.
- Valves: Valves control the flow and direction of the compressed air within the system. They can be manually operated or automated, allowing for precise control over pneumatic tools and actuators. Different types of valves, such as solenoid valves and directional control valves, play specific roles in managing airflow and pressure.
- Actuators: These devices convert the energy from compressed air into mechanical motion. Common types of actuators include cylinders, which can extend and retract to perform tasks such as lifting or pushing. The choice of actuator affects the speed and force of the motion produced.
- Tubing and Fittings: These components transport compressed air from the compressor to the tools and actuators. The choice of tubing material can affect the system’s efficiency and performance, as different materials have varying resistance to pressure and temperature.
Pneumatic systems operate based on the principles of fluid dynamics and pressure differentials. When compressed air is released from the storage tank, it flows through the valves and into the actuators, creating motion. This process is efficient and allows for rapid response times, making pneumatic systems ideal for various applications.
How Do Pneumatic Systems Work?
The operation of pneumatic systems relies on the conversion of compressed air into mechanical energy. Here’s a step-by-step breakdown of how these systems function:
- Compression: The air compressor draws in ambient air and compresses it, increasing its pressure and storing it in a tank. The compressor’s motor powers the compression process, and the efficiency of this step is crucial for the overall performance of the pneumatic system.
- Control: Valves regulate the flow of compressed air, directing it to the appropriate actuators or tools as needed. For instance, a solenoid valve can be activated electrically to open or close, controlling the air supply to a specific actuator.
- Actuation: When the compressed air reaches the actuator, it creates motion. For example, in a pneumatic cylinder, the air pressure pushes a piston, causing it to extend or retract. This motion can be used to perform various tasks, such as moving objects, applying force, or controlling machinery.
- Exhaust: After performing work, the air is released back into the atmosphere, often through exhaust ports in the valves. This exhaust process is essential for maintaining system pressure and ensuring that the actuators can reset for the next cycle.
This cycle allows pneumatic systems to perform tasks quickly and efficiently, making them suitable for a wide range of applications.
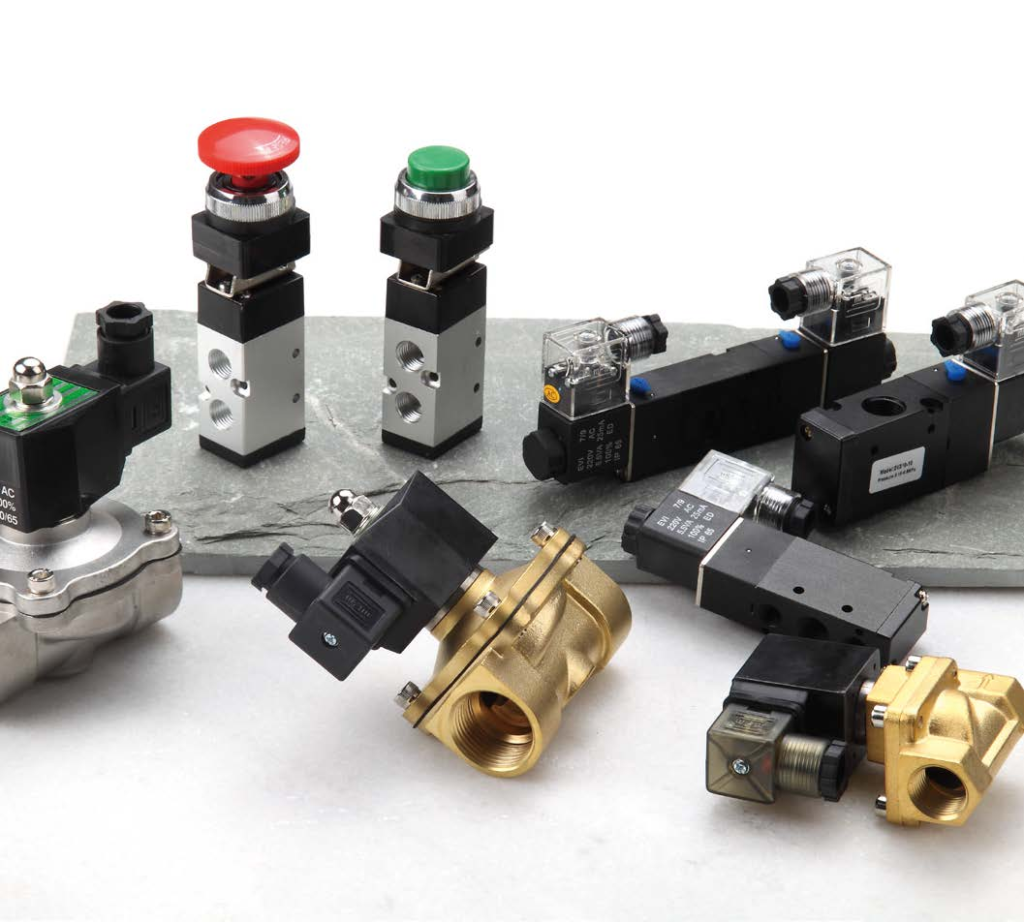
Are Pneumatic Systems Mechanical or Electrical?
Pneumatic systems are primarily classified as mechanical systems. This classification stems from their reliance on mechanical components and the conversion of air pressure into mechanical motion. Unlike electrical systems, which use electrical energy to power motors and devices, pneumatic systems utilize the physical properties of compressed air to generate force and movement.
Comparison with Electrical Systems
- Energy Source: Pneumatic systems use compressed air as their energy source, while electrical systems rely on electrical energy. This fundamental difference affects how each system is designed and operated.
- Operation: Pneumatic systems operate through the movement of air, creating mechanical motion, whereas electrical systems use motors and electrical circuits to perform tasks. This distinction is crucial when considering the application of each system type.
- Components: Pneumatic systems consist of mechanical components such as compressors, valves, and actuators, while electrical systems include motors, switches, and wiring. The choice of components influences the system’s performance and maintenance requirements.
Understanding this distinction is essential for selecting the right system for specific applications, as each type has its advantages and disadvantages.
What Are the Key Differences Between Pneumatic and Electrical Systems?
When comparing pneumatic and electrical systems, several key differences emerge:
- Speed and Response Time: Pneumatic systems typically offer faster response times due to the rapid movement of compressed air. This makes them ideal for applications requiring quick actuation, such as in assembly lines.
- Power-to-Weight Ratio: Pneumatic tools are often lighter than their electric counterparts, making them easier to handle and reducing operator fatigue. This is particularly beneficial in environments where tools are used for extended periods.
- Maintenance: Pneumatic systems generally require less maintenance than electrical systems, as they have fewer moving parts and are less prone to overheating. This can lead to lower operational costs over time.
- Safety: Pneumatic systems are safer in environments where moisture is present, as they do not pose the same electrical hazards as electric systems. This makes them suitable for applications in wet or hazardous environments.
- Cost: Pneumatic systems can be more cost-effective to install and operate, especially in applications where high power is needed without the complexity of electrical systems. The initial investment and ongoing operational costs should be considered when choosing between the two.
In What Applications Are Pneumatic Systems Preferred Over Electrical Systems?
Pneumatic systems excel in various applications across multiple industries. Here are some scenarios where pneumatic systems are often preferred:
- Manufacturing: In assembly lines, pneumatic systems automate processes, providing quick and precise movements for tasks such as fastening and material handling. The ability to control multiple actuators simultaneously enhances productivity.
- Automotive: Pneumatic tools, such as impact wrenches and spray guns, are widely used in automotive assembly and repair, offering high power and efficiency. The lightweight nature of pneumatic tools allows for easier maneuverability in tight spaces.
- Food and Beverage: Pneumatic systems are used for packaging and bottling processes, where hygiene and safety are paramount. The absence of electrical components reduces contamination risks, making pneumatic systems ideal for food handling.
- Construction: Pneumatic tools like nail guns and jackhammers enhance productivity on job sites, allowing for rapid and efficient work. The durability and reliability of pneumatic tools make them a staple in construction applications.
What Are the Benefits of Using Pneumatic Systems?
Pneumatic systems offer numerous advantages that make them a popular choice in various applications:
- Speed: Pneumatic systems can operate at high speeds, allowing for rapid task completion and increased productivity. This is particularly beneficial in high-volume production environments.
- Reliability: With fewer moving parts and lower maintenance requirements, pneumatic systems tend to be more reliable over time. This reliability translates to less downtime and increased operational efficiency.
- Safety: The use of compressed air reduces the risk of electrical hazards, making pneumatic systems safer in many environments. This is especially important in industries where safety is a top priority.
- Flexibility: Pneumatic systems can be easily reconfigured to accommodate different tasks, making them adaptable to changing production needs. This flexibility allows businesses to respond quickly to market demands.
- Cost-Effectiveness: Pneumatic systems are often less expensive to install and maintain compared to hydraulic or electrical systems, providing a budget-friendly solution for many businesses.
What Are the Common Challenges Associated with Pneumatic Systems?
While pneumatic systems offer many benefits, they also come with challenges that users should be aware of:
- Air Leaks: Leaks in the system can lead to reduced efficiency and increased operational costs. Regular maintenance and inspection of fittings and tubing are essential to prevent leaks.
- Pressure Drops: Inadequate pressure can lead to reduced performance. Ensuring that the system is properly sized and that there are no blockages in the tubing is crucial for maintaining optimal performance.
- Equipment Failures: Like any system, pneumatic components can fail. Implementing a routine maintenance schedule can help identify potential issues before they lead to significant downtime.
- Noise: Pneumatic systems can be noisy, which may require soundproofing measures in certain environments. Addressing noise levels is important for maintaining a comfortable working environment.
By addressing these challenges proactively, you can maintain the efficiency and reliability of your pneumatic systems.
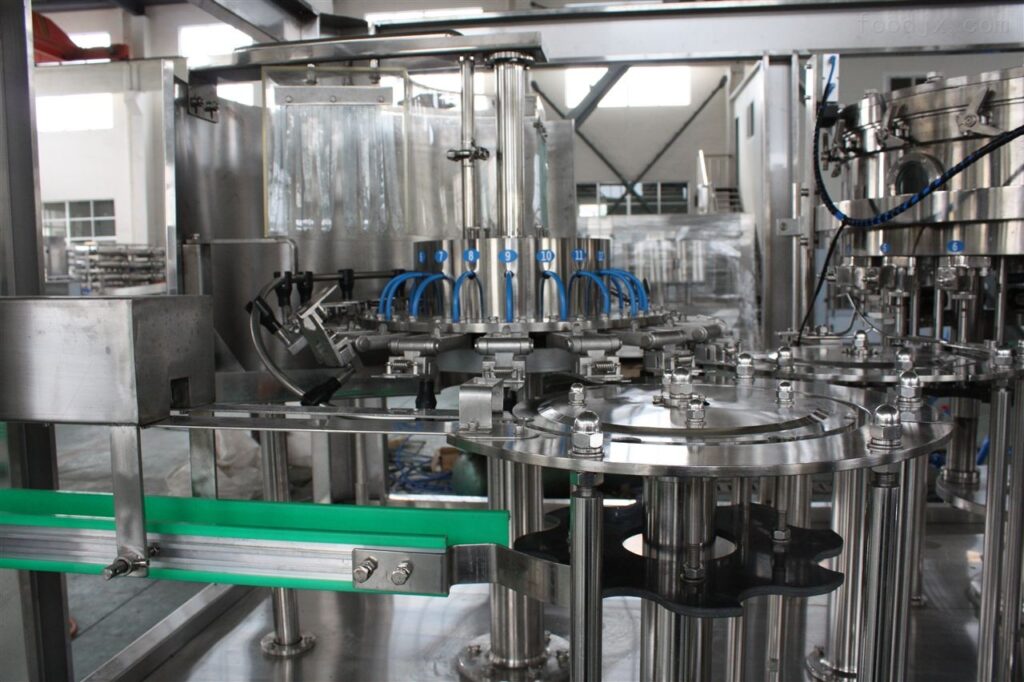
Conclusion
Pneumatic systems are primarily classified as mechanical systems, utilizing compressed air to perform a wide range of tasks across various industries. Understanding the nature of pneumatic systems and their advantages can help you make informed decisions about their implementation in your operations. Whether you are looking to improve efficiency, safety, or productivity, pneumatic solutions can provide the answers you need.
If you have questions or need assistance in selecting pneumatic solutions for your operations, feel free to reach out. With the right knowledge and resources, you can ensure that your pneumatic systems operate smoothly and effectively, ultimately leading to greater success in your business endeavors.