When it comes to pneumatic systems, the choice of fittings is crucial for ensuring optimal performance, safety, and longevity. A common question that arises is whether brass fittings are suitable for use with compressed air. With over dozes years of experience in the industry, I can confidently assert that brass fittings can be an excellent choice for many applications, but there are important considerations to keep in mind. This article will provide a comprehensive overview of brass fittings, their benefits, limitations, and best practices for installation and maintenance, ensuring you have all the information you need to make an informed decision.
What Are Brass Fittings?
Brass fittings are components made from an alloy of copper and zinc, known for their strength, corrosion resistance, and malleability. The specific composition of brass can vary, but it typically contains around 60% copper and 40% zinc, which gives it its distinctive properties. Brass fittings come in various forms, including elbows, tees, couplings, and adapters, making them versatile for different applications. In pneumatic systems, brass fittings are often used to connect tubing and hoses, providing a secure and leak-free connection.

The Composition and Properties of Brass
The unique properties of brass stem from its composition. The copper content provides excellent thermal and electrical conductivity, while zinc enhances strength and corrosion resistance. This combination makes brass fittings particularly suitable for environments where moisture is present, as they can withstand the corrosive effects of water and air. Additionally, brass is easy to machine, allowing for precise manufacturing of fittings that meet specific requirements.
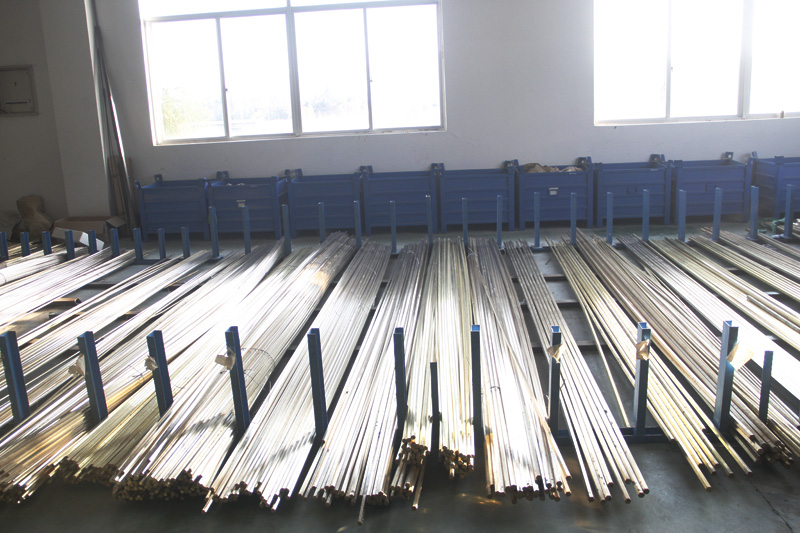
Are Brass Fittings Suitable for Compressed Air?
Yes, brass fittings are generally suitable for compressed air applications. Their robust construction allows them to handle the pressures typically found in pneumatic systems, which can range from a few psi to several hundred psi, depending on the application. However, it’s essential to consider the specific requirements of your system, including pressure ratings and environmental conditions.
Pressure Ratings and Compatibility
Brass fittings are designed to withstand high pressures, making them a reliable choice for many compressed air applications. However, it’s crucial to ensure that the fittings you select are rated for the specific pressures in your system. Always check the manufacturer’s specifications to avoid potential failures. Additionally, consider the temperature range of your application, as extreme temperatures can affect the performance of brass fittings.
What Are the Benefits of Using Brass Fittings for Compressed Air?
- Corrosion Resistance and Durability: Brass is naturally resistant to corrosion, which is crucial in pneumatic systems where moisture can be present. This resistance helps maintain the integrity of the fittings over time, reducing the risk of leaks and failures. Unlike some other materials, brass does not rust, making it a reliable choice for long-term use.
- High Strength: Brass fittings are known for their strength and ability to withstand high pressures without deforming. This makes them ideal for applications where reliability is paramount. The tensile strength of brass allows it to maintain its shape and function even under stress, ensuring a secure connection in your pneumatic system.
- Cost-Effectiveness: Compared to other materials like stainless steel, brass fittings are often more affordable while still providing excellent performance. This cost-effectiveness makes them a popular choice for many businesses, especially in applications where budget constraints are a consideration.
- Ease of Installation: Brass fittings are relatively easy to install, thanks to their compatibility with standard tools and techniques. This ease of use can save time and labor costs during installation, making them an attractive option for both DIY enthusiasts and professionals.
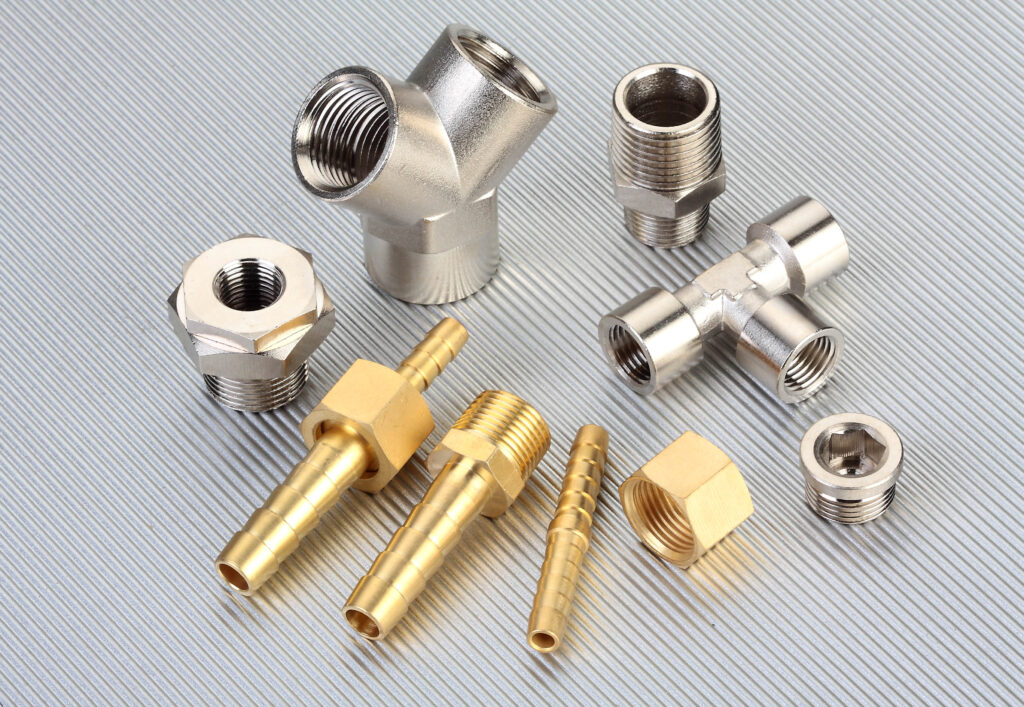
Are There Any Limitations or Concerns with Brass Fittings?
While brass fittings have many advantages, there are some limitations to consider:
- Dezincification: In certain environments, particularly where water is present, brass can undergo a process called dezincification, where zinc leaches out of the alloy, leading to weakened fittings. This is more common in low-flow or stagnant water conditions. To mitigate this risk, it’s essential to choose high-quality brass fittings specifically designed for pneumatic applications, often labeled as “dezincification-resistant” or “DZR” fittings.
- Pressure Limitations: Although brass fittings can handle high pressures, it’s crucial to ensure that the fittings you select are rated for the specific pressures in your system. Always check the manufacturer’s specifications to avoid potential failures. Using fittings beyond their rated capacity can lead to catastrophic failures, resulting in downtime and costly repairs.
- Comparison with Alternatives: While brass is a strong contender, other materials like aluminum and stainless steel may offer advantages in specific applications, such as weight savings or enhanced corrosion resistance. For instance, aluminum fittings are lighter and may be preferred in applications where weight is a concern, while stainless steel fittings provide superior corrosion resistance in harsh environments. It’s worth evaluating your options based on your unique needs.

How to Properly Install Brass Fittings in Compressed Air Systems?
Proper installation is key to ensuring the longevity and reliability of brass fittings. Here’s a step-by-step guide:
- Prepare the Components: Ensure that all surfaces are clean and free from debris. This helps create a secure seal. Use a clean cloth to wipe down the threads of both the fitting and the mating component.
- Use the Right Tools: Utilize appropriate tools for tightening fittings, such as wrenches or pliers, to avoid damaging the fittings. Avoid using excessive force, as this can lead to stripping the threads or cracking the fitting.
- Follow Torque Specifications: Adhere to the manufacturer’s torque specifications to prevent over-tightening, which can lead to cracks or leaks. If torque specifications are not available, a general rule of thumb is to tighten fittings hand-tight plus a quarter turn.
- Check for Leaks: After installation, conduct a leak test by applying a soap solution to the joints. Bubbles will indicate any leaks that need to be addressed. If leaks are detected, re-tighten the fittings or replace them if necessary.
Maintenance Tips for Brass Fittings in Pneumatic Systems
Regular maintenance is essential to ensure the continued performance of brass fittings:
- Inspect Regularly: Periodically check fittings for signs of wear, corrosion, or leaks. Early detection can prevent more significant issues down the line. Look for discoloration, pitting, or any signs of moisture around the fittings.
- Clean as Needed: If you notice any buildup or debris, clean the fittings gently to maintain optimal performance. Use a soft brush or cloth to remove any dirt or grime, and avoid harsh chemicals that could damage the brass.
- Replace When Necessary: If you observe any signs of damage or degradation, replace the fittings promptly to avoid system failures. Keeping a stock of common fittings on hand can help minimize downtime in case of unexpected failures.
Conclusion
In summary, brass fittings can be a reliable and cost-effective choice for compressed air applications, provided you understand their benefits and limitations. By following best practices for installation and maintenance, you can ensure that your pneumatic systems operate efficiently and safely. If you have any questions or need further assistance with selecting the right fittings for your application, don’t hesitate to reach out. Your success in pneumatic systems is my priority, and I’m here to help you navigate the complexities of fittings and tubings. With the right knowledge and tools, you can confidently choose brass fittings for your compressed air needs, ensuring a durable and effective solution for your pneumatic systems.