In the world of pneumatic systems, air pressure fittings are essential components that facilitate the flow of compressed air through various parts of the system. Choosing the right type of fitting is crucial for ensuring efficiency, safety, and reliability. With a variety of fittings available, understanding their unique characteristics and applications can help you make informed decisions that enhance your system’s performance. This article will provide a comprehensive overview of the different types of air pressure fittings, their principles of operation, and practical insights to help you select the best options for your needs.
What Are Air Pressure Fittings?
Air pressure fittings are specialized connectors used in pneumatic systems to join hoses, tubes, and other components. They are designed to create a secure, leak-free connection that allows compressed air to flow efficiently. The right fitting not only ensures the integrity of the system but also contributes to its overall performance and longevity.
What Are the Main Types of Air Pressure Fittings?
There are several types of air pressure fittings commonly used in the industry, each designed for specific applications and requirements. Let’s explore the main types in detail:
1. Push-to-Connect Fittings
Description and Working Principle:
Push-to-connect fittings, also known as push-in fittings, are designed for quick and easy installation. The tubing is simply pushed into the fitting, where a series of internal grips secure it in place. This design eliminates the need for additional tools or clamps, making it a popular choice for many applications.
Advantages:
- Ease of Use: The installation process is straightforward, allowing for rapid assembly and disassembly.
- Reusability: These fittings can be disconnected and reused without damage, making them cost-effective over time.
Common Applications:
Push-to-connect fittings are widely used in automation, robotics, and general pneumatic applications where quick assembly and disassembly are needed. They are particularly beneficial in environments where frequent changes to the system configuration are required.

2. Push-On Fittings
Description and Working Principle:
Push-on fittings are designed to fit snugly onto the tubing without the need for clamps or additional tools. The tubing is simply pushed onto the fitting, creating a secure connection through friction.
Benefits:
- Simplicity: They are easy to install and remove, making them suitable for temporary setups or applications where frequent changes are necessary.
- Cost-Effectiveness: Generally less expensive than other fitting types, making them an economical choice for low-pressure applications.
Typical Applications:
Push-on fittings are often used in low-pressure applications, such as air tools, light-duty pneumatic systems, and situations where quick connections are advantageous.
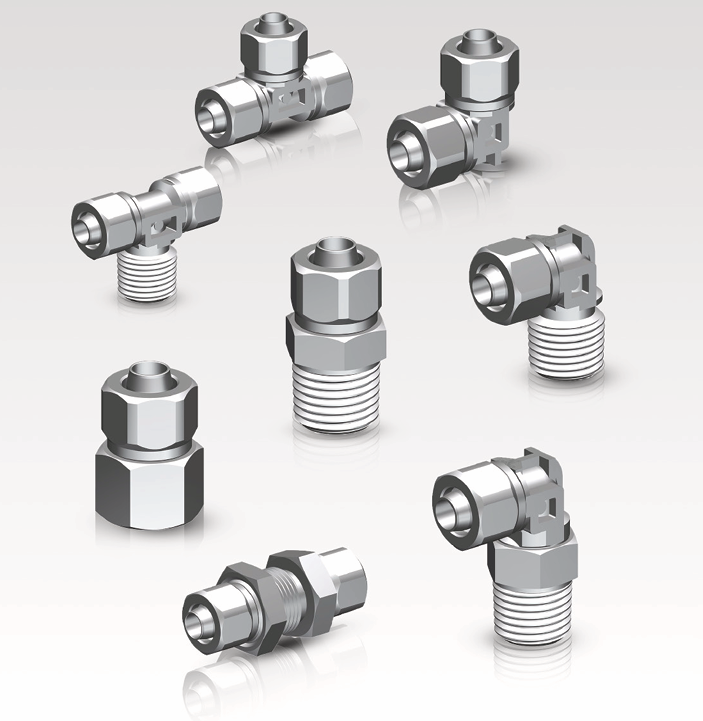
3. Barbed Fittings
Description and Working Principle:
Barbed fittings feature a series of ridges or “barbs” that grip the tubing when it is pushed onto the fitting. This design creates a secure connection that is resistant to pull-off, making it ideal for various applications.
Advantages:
- Secure Connection: The barbs provide a strong grip, reducing the risk of disconnection, even under pressure.
- Versatility: They can be used with various types of tubing materials, including rubber, plastic, and silicone.
Common Uses:
Barbed fittings are frequently found in applications involving fluids, such as in automotive systems, agricultural equipment, and HVAC systems. Their ability to create a tight seal makes them suitable for both air and liquid applications.

4. Threaded Fittings
Description and Working Principle:
Threaded fittings come in various types, including National Pipe Thread (NPT) and British Standard Pipe (BSP). These fittings are designed to screw into place, providing a strong and leak-proof connection. The threads create a mechanical bond that holds the fitting securely in position.
Benefits:
- Strong Connections: The threaded design ensures a tight fit, making them suitable for high-pressure applications where leaks could be catastrophic.
- Variety: Available in different sizes and materials, threaded fittings can be tailored to meet specific application requirements.
Applications:
Threaded fittings are commonly used in industrial applications where high pressure and durability are required, such as in compressors, hydraulic systems, and heavy machinery. Their robust design makes them ideal for environments where reliability is critical.

5. Quick Coupler Fittings
Description and Working Principle:
Quick coupler fittings allow for rapid connection and disconnection of hoses and tools. They typically feature a simple push-button mechanism that enables quick changes without the need for tools. This design is particularly useful in applications where equipment needs to be frequently swapped out.
Advantages:
- Fast Operation: Ideal for applications where tools need to be frequently connected and disconnected, reducing downtime.
- Convenience: The ability to quickly change hoses or tools enhances productivity in dynamic work environments.
Typical Applications:
Quick coupler fittings are often used in mobile equipment, air tools, and any application requiring frequent hose changes, such as in construction, manufacturing, and automotive repair.

How to Choose the Right Air Pressure Fitting?
Selecting the right air pressure fitting involves considering several factors:
- Pressure Ratings: Ensure the fitting can handle the maximum pressure of your system. Each fitting type has a specified pressure rating, and exceeding this can lead to failure.
- Material Compatibility: Choose materials that are compatible with the fluids and gases in your application to prevent degradation. For example, certain plastics may not withstand high temperatures or aggressive chemicals.
- Application Requirements: Consider the specific needs of your application, such as the need for quick connections, the environment in which the fitting will be used, and the type of tubing being employed.
Consulting manufacturer specifications and guidelines can provide valuable insights into the best fitting for your needs.
What Are the Common Materials Used for Air Pressure Fittings?
Air pressure fittings are made from various materials, each with its own advantages and disadvantages:
- Brass: Known for its durability and resistance to corrosion, brass fittings are commonly used in high-pressure applications. They provide excellent strength and are suitable for a wide range of temperatures.
- Plastic: Lightweight and cost-effective, plastic fittings are suitable for low-pressure applications but may not withstand high temperatures or harsh chemicals. They are often used in applications where weight is a concern.
- Stainless Steel: Offers excellent corrosion resistance and strength, making it ideal for harsh environments. Stainless steel fittings are often used in food processing, pharmaceuticals, and other applications where hygiene is critical.
Choosing the right material is essential for ensuring the longevity and reliability of your fittings.
How to Maintain Air Pressure Fittings for Longevity?
To keep your air pressure fittings in optimal condition, consider the following best practices:
- Regular Inspections: Periodically check fittings for signs of wear, corrosion, or leaks. Early detection can prevent more significant issues down the line. Look for any signs of discoloration or damage that may indicate a problem.
- Proper Installation: Ensure that fittings are installed correctly to avoid leaks and ensure a secure connection. Follow manufacturer guidelines for torque specifications and installation procedures.
- Cleaning: Keep fittings clean and free from debris to maintain their functionality. Regularly clean the exterior of fittings and check for any buildup that could affect performance.
Troubleshooting Common Issues with Air Pressure Fittings
Even with proper maintenance, issues can arise. Here are some common problems and their solutions:
- Leaks: If you notice air escaping from a fitting, check for loose connections or damaged seals. Tightening or replacing the fitting may resolve the issue. If the problem persists, inspect the tubing for cuts or abrasions.
- Pressure Drops: A sudden drop in pressure could indicate a blockage or malfunctioning valve. Inspect the system for obstructions and ensure all components are functioning correctly. Regularly monitor pressure levels to identify trends that may indicate a problem.
- Contamination: Contaminants in the air supply can lead to performance issues and damage to components. Implementing a filtration system can help prevent this problem. Regularly check and replace filters to maintain air quality.
Conclusion
In summary, understanding the different types of air pressure fittings is essential for optimizing the performance and reliability of your pneumatic systems. Each fitting type has its unique advantages and applications, making it crucial to select the right one for your specific needs. By considering factors such as pressure ratings, material compatibility, and application requirements, you can ensure that your pneumatic system operates efficiently and effectively.
If you have any questions or experiences to share regarding air pressure fittings, feel free to reach out. Your insights can contribute to a better understanding of this essential aspect of pneumatic applications, helping others navigate their choices with confidence.