In the world of pneumatic systems, the choice of fittings can make or break the efficiency and reliability of your setup. Among the various types of fittings available, push-to-connect fittings have gained immense popularity due to their ease of use and versatility. However, selecting the right push-to-connect fitting is not as straightforward as it may seem. It requires a thorough understanding of several key factors that can significantly impact the performance of your pneumatic system. In this article, I’ll delve into these factors, providing you with the insights needed to make informed decisions that will meet your specific application requirements.
What Are Push-to-Connect Fittings?
Push-to-connect fittings, also known as push-in fittings, are designed to create a secure and leak-free connection between tubing and components in pneumatic systems without the need for tools. The mechanism is simple: the tubing is pushed into the fitting, which then grips the tubing with a series of internal teeth and seals it with an O-ring. This design allows for quick installation and disconnection, making push-to-connect fittings ideal for applications where frequent changes or adjustments are necessary. Their reliability and ease of use have made them a staple in various industries, including manufacturing, automotive, and medical applications.
1. What is the Application Environment?
The first step in selecting the right push-to-connect fitting is to understand the application environment. The operating conditions—such as temperature, pressure, and exposure to chemicals—play a crucial role in determining the suitability of a fitting. For instance, if your application involves high temperatures, you’ll need fittings made from materials that can withstand thermal expansion and degradation. Similarly, if the fittings will be exposed to aggressive chemicals, selecting materials that offer chemical resistance is essential. Always assess the specific environment in which the fittings will be used, whether it’s in an industrial setting, automotive application, or medical environment, to ensure compatibility and reliability.
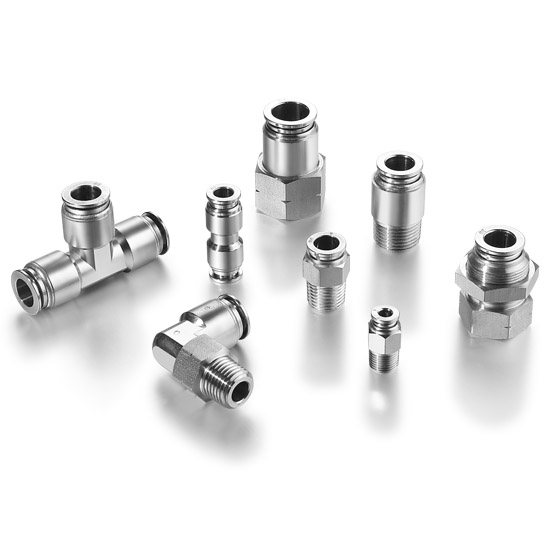
2. What Type of Tubing Will Be Used?
The type of tubing you plan to use is another critical factor in selecting the right push-to-connect fitting. Different fittings are designed to work with specific tubing materials, such as polyurethane (PU), nylon, polyethylene (PE), or PTFE. Each material has its own characteristics, including flexibility, chemical resistance, and pressure ratings. For example, PU tubing is known for its flexibility and resistance to abrasion, making it suitable for dynamic applications, while PTFE tubing offers excellent chemical resistance but is less flexible. Ensure that the fitting you choose is compatible with the tubing material to prevent leaks and ensure optimal performance. Using a fitting designed for rigid tubing with flexible tubing can lead to connection failures, so always verify compatibility.

3. What is the Required Flow Rate?
Flow rate is a vital consideration when selecting push-to-connect fittings. The fitting size and design must match the system’s flow requirements to ensure efficient operation. If the flow rate is too high for a fitting, it can lead to pressure drops and reduced system performance. Conversely, using a fitting that is too large can result in unnecessary costs and space usage. To determine the appropriate fitting size, calculate the required flow rate for your application. This involves understanding the system’s overall design, including the diameter of the tubing and the expected flow conditions. Consult manufacturer specifications to find a fitting that meets those needs, ensuring that it can handle the required flow without compromising performance.

4. What Are the Pressure Requirements?
Every pneumatic system operates under specific pressure conditions, and it’s essential to select fittings that can handle these pressures. Push-to-connect fittings come with different pressure ratings, and using a fitting that cannot withstand the system’s pressure can lead to catastrophic failures. Always check the pressure rating of the fitting and ensure it exceeds the maximum pressure your system will encounter. This precaution will help maintain system integrity and prevent leaks or ruptures. Additionally, consider the pressure fluctuations that may occur during operation; selecting a fitting with a higher pressure rating can provide an extra margin of safety.
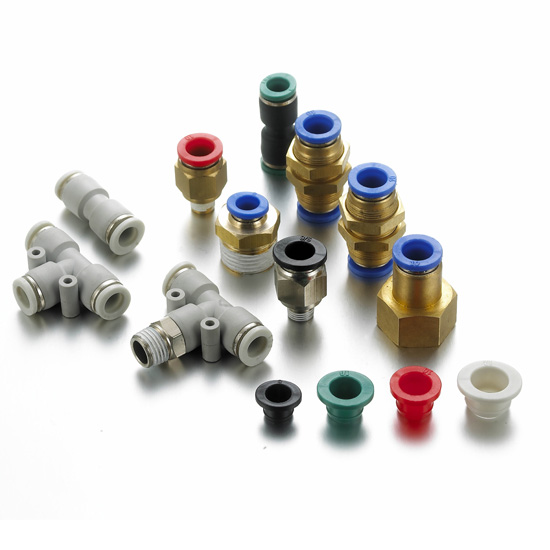
5. What Size Fitting is Needed?
Selecting the correct fitting size is crucial for ensuring a secure and leak-free connection. The size of the fitting must match the diameter of the tubing being used. To determine the right size, measure the outer diameter of the tubing and consult the fitting specifications. Many manufacturers provide sizing charts that can help you find the perfect match. Remember, using the wrong size fitting can lead to connection issues, including leaks and reduced system efficiency. Additionally, consider the space available for installation; in tight spaces, a compact fitting design may be necessary to facilitate proper installation and maintenance.

6. Are There Any Special Features Required?
Consider whether your application requires any special features in the push-to-connect fittings. Some fittings come with additional functionalities, such as shut-off valves, which can be beneficial for maintenance and safety. Shut-off valves allow you to isolate sections of the system without having to disconnect the tubing, making maintenance easier and safer. Quick disconnect features can also enhance usability, allowing for rapid changes without the need for tools. Assess your specific needs and choose fittings that offer the features that will enhance your system’s performance and ease of use. For example, if your application requires frequent disconnections, investing in quick disconnect fittings can save time and effort.

7. What is the Budget and Quality Consideration?
While it’s tempting to go for the cheapest option, it’s essential to balance cost with quality and reliability. Investing in high-quality push-to-connect fittings can save you money in the long run by reducing the risk of leaks and failures. Look for fittings from reputable manufacturers that offer warranties and have a proven track record in the industry. Consider the total cost of ownership, which includes not only the initial purchase price but also the potential costs associated with maintenance, downtime, and replacements. Remember, the right fitting can enhance system performance and longevity, making it a worthwhile investment.
Conclusion
Selecting the perfect push-to-connect fitting involves careful consideration of various factors, including the application environment, tubing type, flow rate, pressure requirements, fitting size, special features, and budget. By taking the time to assess these elements, you can ensure that you choose fittings that meet your specific needs and enhance the performance of your pneumatic system.