Choosing the right flexible tubing material is a critical decision that can significantly influence the performance, durability, and efficiency of your systems. With a plethora of options available, understanding the unique properties, applications, and limitations of each material is essential. This comprehensive guide will delve into the various materials used for flexible tubing, their characteristics, and how to select the best option for your specific needs, ensuring you have all the information necessary to make an informed decision.
What Are the Common Materials Used for Flexible Tubing?
Flexible tubing is manufactured from several key materials, each offering distinct advantages and disadvantages. Here’s a detailed look at the most common materials:
Polyurethane (PU)
Polyurethane tubing is renowned for its exceptional flexibility and resilience. It can withstand repeated bending and flexing without kinking, making it ideal for applications that require tight bends and dynamic movement. PU tubing is also resistant to abrasion, which prolongs its lifespan in environments where wear and tear are common.
Applications: PU tubing is widely used in pneumatic systems, robotics, and applications involving air and fluid transfer. Its ability to maintain performance under varying temperatures and pressures makes it a versatile choice.

Nylon
Nylon tubing is celebrated for its strength and durability. It exhibits excellent resistance to chemicals, making it suitable for applications where exposure to harsh substances is a concern. Nylon is also capable of withstanding high pressures, which is crucial in many industrial applications.
Applications: Commonly found in automotive fuel lines, hydraulic systems, and industrial machinery, nylon tubing is a go-to choice for applications requiring robust performance and reliability.
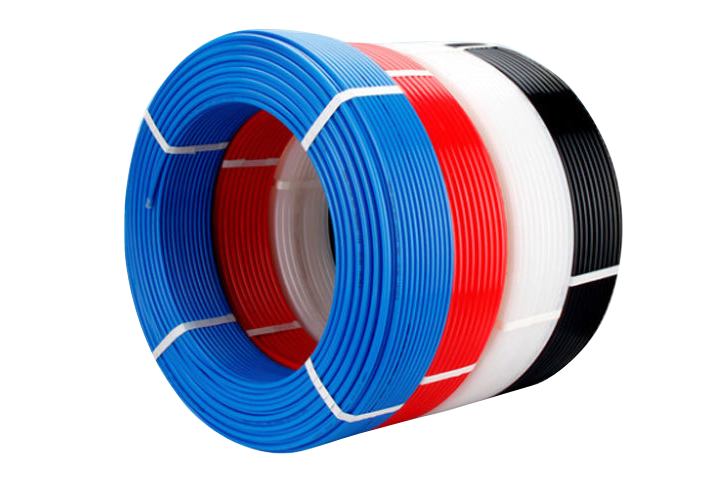
Polyethylene (PE)
Polyethylene tubing is lightweight, flexible, and cost-effective. While it may not offer the same level of chemical resistance as nylon or PU, it is still suitable for many general-purpose applications. PE tubing is easy to handle and install, making it a popular choice for various projects.
Applications: PE tubing is often used in irrigation systems, water lines, and other applications where cost-effectiveness is essential without compromising too much on performance.
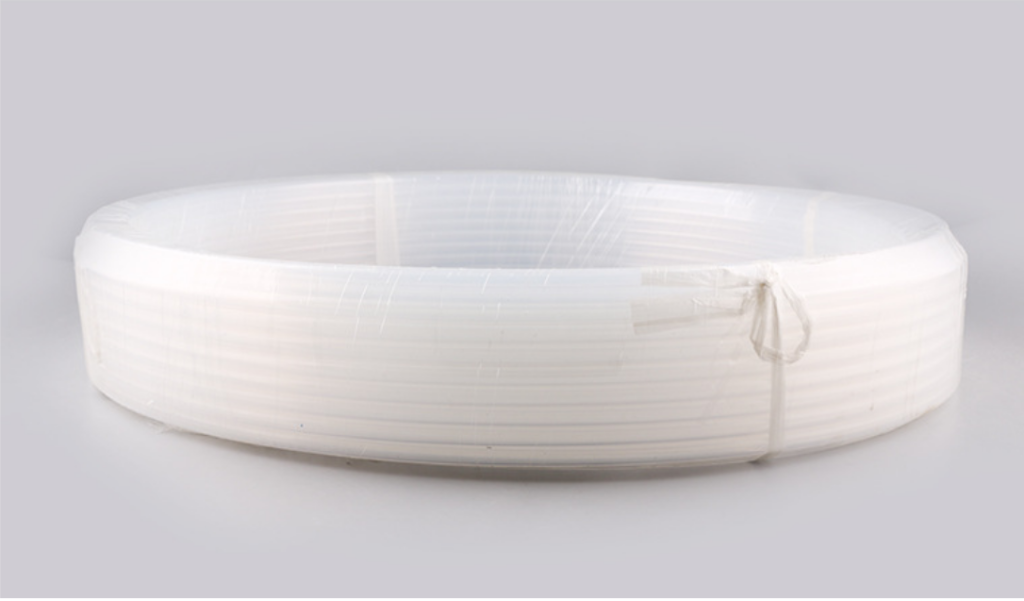
Polytetrafluoroethylene (PTFE)
PTFE tubing is known for its outstanding chemical resistance and ability to withstand high temperatures. This material is non-reactive, making it ideal for applications involving aggressive chemicals or extreme conditions. PTFE’s low friction properties also make it an excellent choice for applications requiring smooth fluid flow.
Applications: PTFE tubing is frequently used in the pharmaceutical industry, food processing, and chemical handling, where purity and resistance to contamination are paramount.
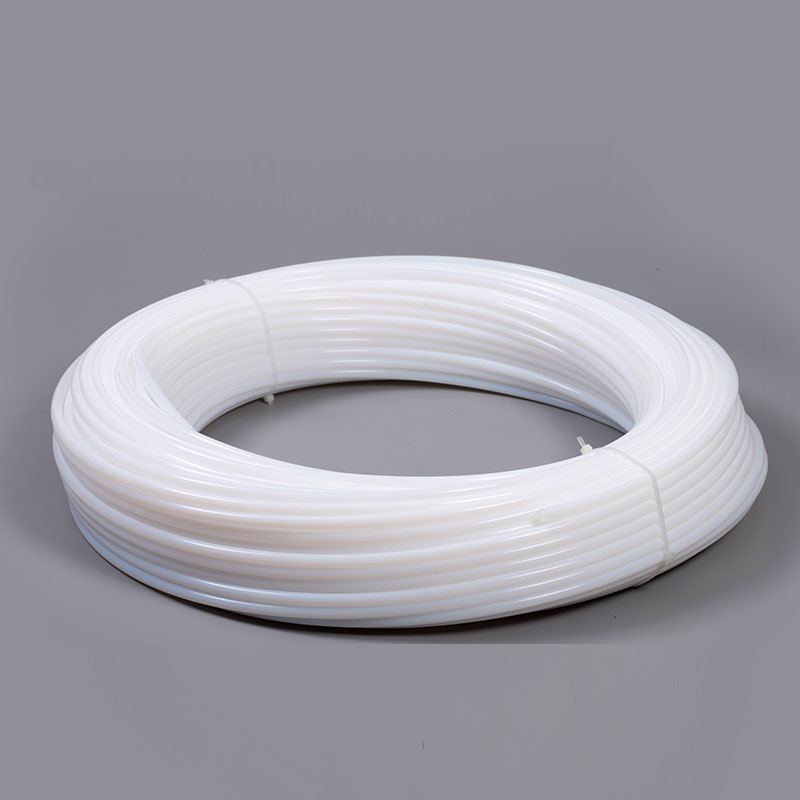
How Material Properties Affect Performance?
The performance of flexible tubing is heavily influenced by the material used. Here’s how different properties can impact your choice:
Flexibility and Bend Radius
Flexibility is crucial in applications where tubing must navigate tight spaces or undergo frequent movement. PU tubing excels in this regard, allowing for sharp bends without kinking. In contrast, nylon tubing, while strong, may not offer the same level of flexibility, which could limit its use in dynamic applications.
Temperature and Pressure Resistance
Each material has a specific temperature and pressure rating. For instance, PTFE can handle extreme temperatures and pressures, making it suitable for high-stakes applications. Conversely, PE tubing may not perform well under high temperatures, leading to potential failure. Always check the specifications to ensure the tubing can withstand the conditions it will face.
Chemical Compatibility
Chemical resistance is a critical factor in selecting tubing for applications involving corrosive substances. Nylon and PTFE offer excellent resistance to a wide range of chemicals, while PE may degrade when exposed to certain solvents. Understanding the chemical environment of your application is essential to avoid premature failure.
What Are the Key Factors to Consider When Choosing Flexible Tubing?
When selecting flexible tubing, consider the following factors to ensure you make the best choice for your application:
Application Requirements
Evaluate the specific requirements of your application, including pressure, temperature, and chemical exposure. For example, if your application involves high pressure and temperature, PTFE or nylon tubing may be the best options. Conversely, for low-pressure applications, PE tubing could suffice.
Environmental Conditions
Consider the environment in which the tubing will operate. Will it be exposed to UV light, extreme temperatures, or abrasive materials? PU tubing offers excellent UV resistance, while nylon provides superior abrasion resistance. Understanding these environmental factors will help you choose a material that can withstand the conditions it will face.
Regulatory Compliance
Depending on your industry, you may need to adhere to specific regulations regarding material safety and performance. For food and medical applications, ensure that the tubing is food-grade or medical-grade to prevent contamination and comply with health standards.
How Does the Manufacturing Process Impact Material Selection?
The manufacturing process of flexible tubing can significantly affect its quality and performance. Here are some key points to consider:
Extrusion and Quality Control
Extrusion is a common method used to produce flexible tubing, allowing for consistent wall thickness and flexibility. During the manufacturing process, quality control is paramount. Tubing that undergoes rigorous testing for pressure, temperature, and chemical resistance will perform better in real-world applications. Always choose suppliers who prioritize quality assurance to ensure you receive reliable products.
Customization Options
Many manufacturers offer customization options, allowing you to tailor the tubing to your specific needs. This can include variations in diameter, wall thickness, and even the addition of specific additives for enhanced performance. Customization can be particularly beneficial for unique applications that require specific characteristics.
What Are the Common Applications for Each Type of Flexible Tubing?
Understanding the applications for each type of flexible tubing can help you make a more informed decision based on your specific needs:
- PU Tubing: Ideal for pneumatic systems, robotics, and applications requiring high flexibility and resistance to wear. Its ability to handle dynamic movements makes it a favorite in industries where mobility is essential.
- Nylon Tubing: Commonly used in automotive fuel lines, hydraulic systems, and industrial machinery due to its strength and chemical resistance. Its durability makes it suitable for high-pressure applications.
- PE Tubing: Often found in irrigation systems, water lines, and general-purpose applications where cost-effectiveness is key. Its lightweight nature makes it easy to handle and install.
- PTFE Tubing: Frequently used in the pharmaceutical industry, food processing, and chemical handling due to its superior chemical resistance and high-temperature capabilities. Its non-reactive nature ensures purity in sensitive applications.
What Are the Troubleshooting Tips for Common Issues with Flexible Tubing?
Even the best flexible tubing can encounter issues. Here are some common problems and their solutions:
Kinking
Kinking often occurs when tubing is bent too sharply. To prevent kinking, ensure that the tubing is installed with gentle curves and avoid sharp bends. If kinking does occur, it may compromise the integrity of the tubing, leading to leaks or failure.
Bursting
If the tubing bursts, it may be due to exceeding the pressure rating. Always check the specifications and ensure that the tubing is suitable for your application’s pressure requirements. Regularly inspect the tubing for signs of wear and replace it as needed to prevent catastrophic failures.
Chemical Degradation
If you notice discoloration or brittleness, the tubing may be degrading due to chemical exposure. Always verify compatibility with the chemicals used in your application. If degradation is observed, consider switching to a more chemically resistant material, such as nylon or PTFE.
How to Ensure Proper Installation and Maintenance of Flexible Tubing?
Proper installation and maintenance are crucial for the longevity of flexible tubing. Here are some best practices:
Installation
Ensure that the tubing is cut cleanly and fitted securely to prevent leaks. Use appropriate fittings and connectors to maintain a tight seal. Avoid over-tightening, which can damage the tubing and lead to leaks.
Maintenance
Regularly inspect the tubing for signs of wear, such as cracks or discoloration. Clean the tubing as needed, especially in applications involving food or pharmaceuticals, to prevent contamination. Establish a routine maintenance schedule to ensure the tubing remains in optimal condition.
Conclusion
Selecting the right material for flexible tubing is a critical decision that can impact the success of your application. By understanding the properties of different materials, considering key factors, and following best practices for installation and maintenance, you can make an informed choice that meets your needs.
If you have specific requirements or need personalized advice, don’t hesitate to contact us sales@idealbelltechnology.com