Introduction
Pneumatic fittings are critical components in fluid and air transfer systems, ensuring that compressed air and fluids flow efficiently through various applications. Understanding the different types of fittings is essential for anyone involved in the design, maintenance, or operation of pneumatic systems. The right fitting not only enhances system performance but also improves reliability and safety. In this article, I will provide a comprehensive overview of the three main types of fittings—push-to-connect fittings, threaded fittings, and barbed fittings—detailing their functions, applications, and how to select the most suitable option for your needs.
1. What Are Pneumatic Fittings?
Pneumatic fittings are devices used to connect hoses, tubes, and other components in pneumatic systems. They facilitate the flow of compressed air and fluids, ensuring that the system operates smoothly and efficiently. Fittings come in various designs and materials, each suited for specific applications and operational conditions. The choice of fitting can significantly impact the performance and reliability of the system, making it essential to understand the different types available.
2. What Are the Three Main Types of Fittings?
The three primary types of fittings used in pneumatic systems are push-to-connect fittings, threaded fittings, and barbed fittings. Each type has unique characteristics and is suited for specific applications.
3. What Are Push-to-Connect Fittings?
Push-to-connect fittings, also known as push-in fittings, are designed for quick and easy connections without the need for tools. You simply push the tubing into the fitting, and it locks in place, creating a secure connection.
Advantages of Push-to-Connect Fittings
- Ease of Use: The tool-free operation allows for quick assembly and disassembly, making them ideal for applications where frequent changes are necessary. This feature is particularly beneficial in dynamic environments where time efficiency is crucial.
- Time-Saving: The ability to connect and disconnect quickly reduces downtime, enhancing productivity in fast-paced environments. This is especially important in manufacturing and assembly lines where efficiency is key.
- Versatility: These fittings are available in various sizes and configurations, making them suitable for a wide range of applications, from automotive to industrial settings. They can accommodate different tubing materials, including polyurethane (PU), nylon, and polyethylene (PE).
- Leak-Free Performance: Push-to-connect fittings often feature built-in sealing mechanisms, such as O-rings, which help prevent leaks and maintain system pressure. This ensures that the system operates efficiently without loss of air or fluid.
Common Scenarios for Push-to-Connect Fittings
You’ll often find push-to-connect fittings in applications such as:
- Assembly Lines: Where tools and hoses need to be frequently swapped out to accommodate different tasks.
- Robotics: In robotic systems where quick adjustments are necessary to adapt to changing operational requirements.
- Medical Equipment: Where reliability and quick connections are critical for patient safety and equipment functionality.
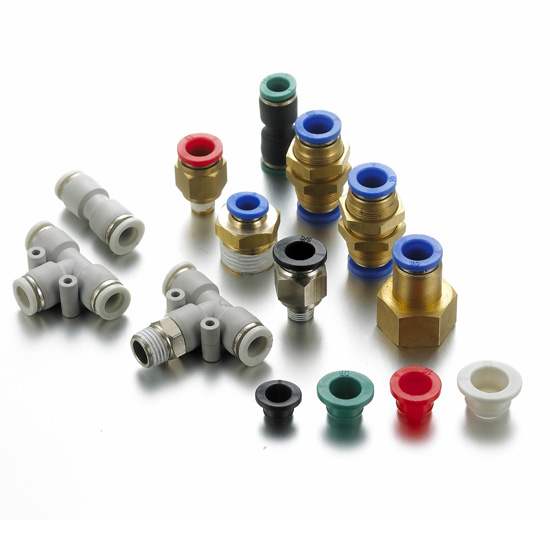
4. What Are Threaded Fittings?
Threaded fittings are designed to create a secure connection using threaded connections. These fittings are commonly used in high-pressure applications where a robust seal is necessary.
Benefits of Threaded Fittings
- High Pressure Tolerance: Threaded fittings can handle high-pressure environments, making them suitable for industrial applications where pressure fluctuations are common. They are often used in hydraulic and pneumatic systems that require a strong, leak-proof connection.
- Durability: Typically made from materials like brass or stainless steel, threaded fittings are resistant to corrosion and wear, ensuring a long service life. This durability is essential in environments where fittings are exposed to harsh conditions.
- Secure Connections: The threaded design provides a strong mechanical connection, reducing the risk of disconnections or leaks. This is particularly important in applications where safety is a concern.
- Variety of Thread Types: Threaded fittings come in various thread types, such as NPT (National Pipe Thread) and BSP (British Standard Pipe), allowing for compatibility with different systems. Understanding the specific thread type required for your application is crucial for ensuring a proper fit.
Common Applications for Threaded Fittings
- Hydraulic Systems: Where high pressure and fluid transfer are critical, such as in construction equipment and industrial machinery.
- Industrial Equipment: In machinery that requires secure and reliable connections, such as compressors and pneumatic tools.
- Pneumatic Tools: Where a strong connection is necessary to maintain performance and prevent leaks.
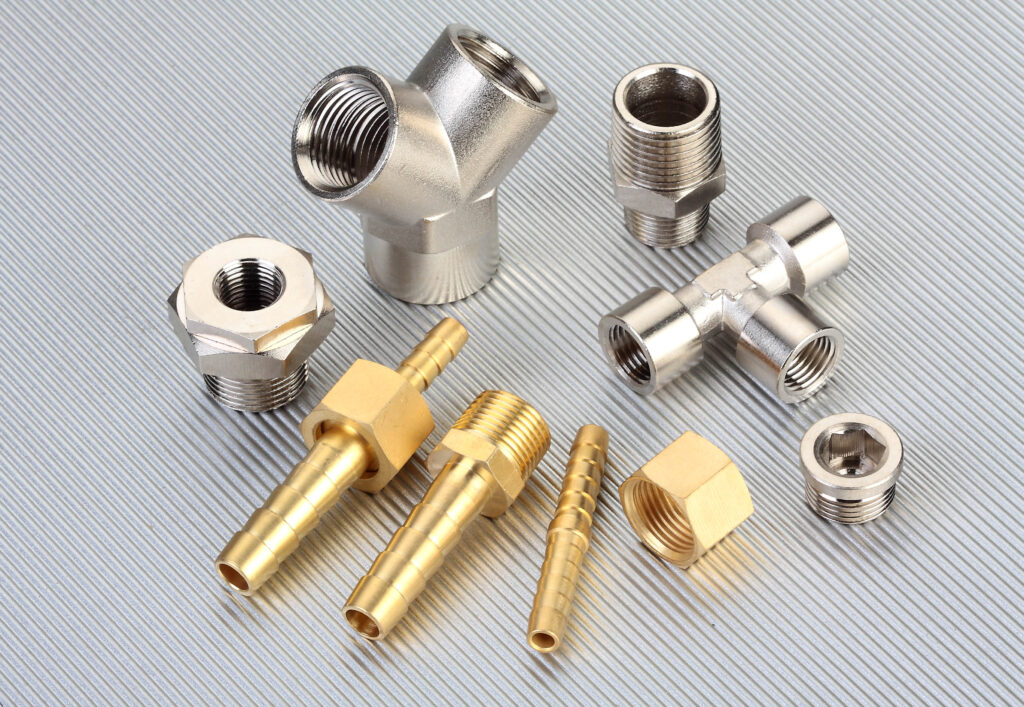
5. What Are Barbed Fittings?
Barbed fittings feature ridges or barbs that grip the tubing when it is pushed onto the fitting. This design creates a secure connection that is particularly effective in low-pressure applications.
Advantages of Barbed Fittings
- Simplicity: Barbed fittings are straightforward to use; simply push the hose onto the fitting, and the barbs hold it in place. This ease of use makes them a popular choice for DIY projects and quick repairs.
- Cost-Effectiveness: Generally less expensive than other types of fittings, making them a budget-friendly option for many applications. Their low cost does not compromise their effectiveness in suitable applications.
- Versatile Applications: Suitable for a variety of tubing materials, including rubber, PVC, and silicone. This versatility allows them to be used in diverse settings, from home plumbing to industrial applications.
- Good for Low-Pressure Systems: Barbed fittings are ideal for applications where pressure is not a primary concern, such as in drainage or irrigation systems. They provide a reliable connection without the need for additional clamps in many cases.
Common Applications for Barbed Fittings
- Garden Hoses: Connecting hoses in irrigation systems, where flexibility and ease of connection are important.
- Aquarium Equipment: Where water flow needs to be managed effectively, ensuring that pumps and filters operate smoothly.
- Low-Pressure Air Systems: In applications where high pressure is not required, such as in pneumatic tools that operate at lower pressures.

6. How to Choose the Right Fitting for Your Application?
Selecting the right fitting involves considering several factors:
- Application Requirements: Assess the specific needs of your application, including pressure ratings, temperature ranges, and the type of media being transported. For example, if you are working with high-pressure air, threaded fittings may be the best choice.
- Compatibility: Ensure that the fitting is compatible with the tubing and other components in your system. Mismatched fittings can lead to leaks and system failures. Check the dimensions, materials, and connection types to ensure a proper fit.
- Environmental Conditions: Consider the operating environment, including temperature, humidity, and exposure to chemicals, as these factors can affect the performance of the fitting. For instance, if the fitting will be exposed to corrosive substances, a material resistant to corrosion should be selected.
- Ease of Installation: If quick assembly and disassembly are important, push-to-connect fittings may be the best option. For applications requiring a more permanent connection, threaded fittings might be more appropriate.
- Maintenance Needs: Evaluate how much maintenance you are willing to perform. Some fittings may require more frequent checks and replacements than others, depending on the application.
- Pressure and Flow Requirements: Consider the pressure and flow requirements of your system. Ensure that the selected fitting can handle the expected pressure and flow rates without compromising performance.
By carefully evaluating these factors, you can select the most appropriate fitting for your pneumatic system, enhancing performance and reliability.
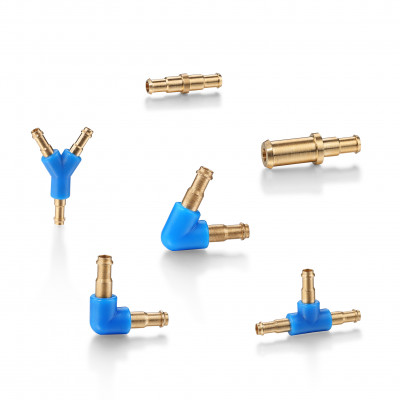
7. What Are Common Troubleshooting Tips for Fittings?
Even with the best fittings, issues can arise. Here are some common problems and their solutions:
- Leaks: If you notice a drop in pressure or performance, check for leaks in hoses, fittings, and connections. Regularly inspect and maintain these components to prevent leaks, as they can significantly impact system efficiency.
- Disconnections: If fittings are frequently disconnecting, ensure that they are properly installed and compatible with the tubing. Consider using fittings designed for higher retention if disconnections are a recurring issue.
- Wear and Tear: Over time, fittings can wear out due to exposure to pressure, temperature, and environmental factors. Regularly inspect fittings for signs of wear, such as cracks or deformation, and replace them as needed to maintain system integrity.
- Incorrect Installation: Ensure that fittings are installed according to the manufacturer’s specifications. Improper installation can lead to leaks and system failures.
8. Conclusion
Understanding the different types of fittings—push-to-connect, threaded, and barbed—is essential for anyone working with pneumatic systems. By selecting the right fitting based on your application’s needs, you can enhance system performance, reduce downtime, and ensure reliable operation. Take the time to evaluate your requirements and choose the fittings that best suit your operations.
I invite you to share your experiences or ask any questions you may have about fittings. Your insights can help others in the community. For more information, check out our additional resources and products related to pneumatic fittings and systems. Let’s enhance our understanding of pneumatic systems together!