Introduction
Air fittings are indispensable components in pneumatic systems, serving as the vital connectors that facilitate the flow of compressed air between various system components. Understanding how air fittings work, the different types available, and their specific applications can significantly enhance the performance and reliability of your pneumatic systems.
1. What Are Air Fittings Used For?
Air fittings are designed to connect various components in a pneumatic system, such as hoses, tubes, valves, and air tools. They ensure a secure and leak-free connection, allowing for the efficient transfer of compressed air throughout the system.
Applications
- Manufacturing: In assembly lines, air fittings are used to connect pneumatic tools that power machinery, enabling efficient production processes. For instance, air fittings connect air drills, impact wrenches, and other tools that require a reliable air supply.
- Automotive: In repair shops, air fittings connect pneumatic tools like impact wrenches and spray guns, facilitating quick and effective repairs. Proper fittings ensure that tools operate at peak performance, reducing the time needed for repairs.
- Construction: Air fittings are essential for connecting air compressors to tools such as nail guns and pneumatic drills, enhancing productivity on job sites. The right fittings can withstand the rigors of construction environments, ensuring durability and reliability.
Benefits
Using the right air fittings can lead to:
- Improved Efficiency: Properly selected fittings minimize air loss, ensuring that tools operate at optimal performance. This efficiency translates to faster job completion and reduced operational costs.
- Reduced Risk of Leaks: High-quality fittings create tight seals that prevent air leaks, which can lead to increased operational costs and safety hazards. Regularly inspecting and maintaining fittings can further reduce the risk of leaks.
- Enhanced Safety: Reliable connections reduce the risk of accidents caused by sudden disconnections or air leaks. Ensuring that all fittings are properly installed and maintained contributes to a safer working environment.

2. What Types of Air Fittings Are There?
There are several types of air fittings, each designed for specific applications and requirements. Common types of air fittings include quick connect, threaded, push-to-connect, and barbed fittings, each serving specific applications in pneumatic systems. Understanding these types can help you choose the right fitting for your needs.
Type of Fitting | Description | Advantages |
---|---|---|
Quick Connect Fittings | Allow for fast and easy connections without tools, featuring a spring-loaded mechanism. | Time-saving and user-friendly, ideal for frequent changes. |
Threaded Fittings | Feature internal or external threads for secure connections, available in various standards (NPT, BSP). | Strong and reliable connections, suitable for high-pressure applications. |
Push-to-Connect Fittings | Enable quick connections by simply pushing the tube into the fitting, often used in modular systems. | Easy to use and versatile, allowing for rapid assembly and disassembly. |
Barbed Fittings | Designed for use with flexible hoses, featuring a barbed end that grips the hose tightly. | Secure grip on hoses, preventing leaks and disconnections. |

3. How Do Air Fittings Work?
Air fittings work by creating a secure connection between different components of a pneumatic system, allowing compressed air to flow efficiently.
Mechanisms
- Quick Connect Fittings: These fittings utilize a spring-loaded mechanism that locks the fitting in place when connected. This design allows for easy disconnection when needed, making them ideal for applications requiring frequent changes. The simplicity of operation reduces downtime and enhances productivity.
- Threaded Fittings: These rely on screw threads to create a tight seal, preventing air leaks. They are often used in high-pressure applications where a secure connection is critical. Proper installation is essential to ensure that the threads are aligned correctly and tightened adequately.
- Push-to-Connect Fittings: These fittings allow for a simple push to connect, making them ideal for quick setups and changes. They are commonly used in modular systems where components need to be frequently rearranged. The ease of use makes them popular in both industrial and DIY applications.
- Barbed Fittings: The barbed design grips the hose tightly, ensuring a secure connection that minimizes the risk of disconnection. They are particularly useful in applications where flexibility is required, such as in automotive and agricultural settings.
Air fittings facilitate the flow of compressed air by creating secure connections between system components, with various mechanisms like quick connect, threaded, and push-to-connect designs.
4. How to Install Air Fittings
Proper installation of air fittings is crucial for ensuring a leak-free and efficient pneumatic system. Here’s a step-by-step guide to help you install air fittings correctly:
- Prepare the Components: Ensure that all surfaces are clean and free of debris. This step is vital to prevent contamination and ensure a proper seal. Use a clean cloth or brush to remove any dirt or dust from the fitting and the connecting components.
- Apply Thread Sealant: For threaded fittings, apply a suitable thread sealant to the male threads. This will help prevent leaks and ensure a tight fit. Be sure to use a sealant that is compatible with the materials of the fitting and the application.
- Connect the Fitting: Securely tighten the fitting by hand or with a tool, depending on the type. Be careful not to overtighten, as this can damage the fitting or the connected component. A snug fit is usually sufficient to create a reliable seal.
- Test for Leaks: After installation, test the connection by running air through the system and checking for leaks. You can use a soap solution to identify any leaks; bubbles will form at the leak points. If you detect any leaks, disconnect the fitting, reapply sealant if necessary, and reconnect.
To install air fittings, clean the surfaces, apply thread sealant if needed, securely connect the fitting, and test for leaks to ensure a proper installation.
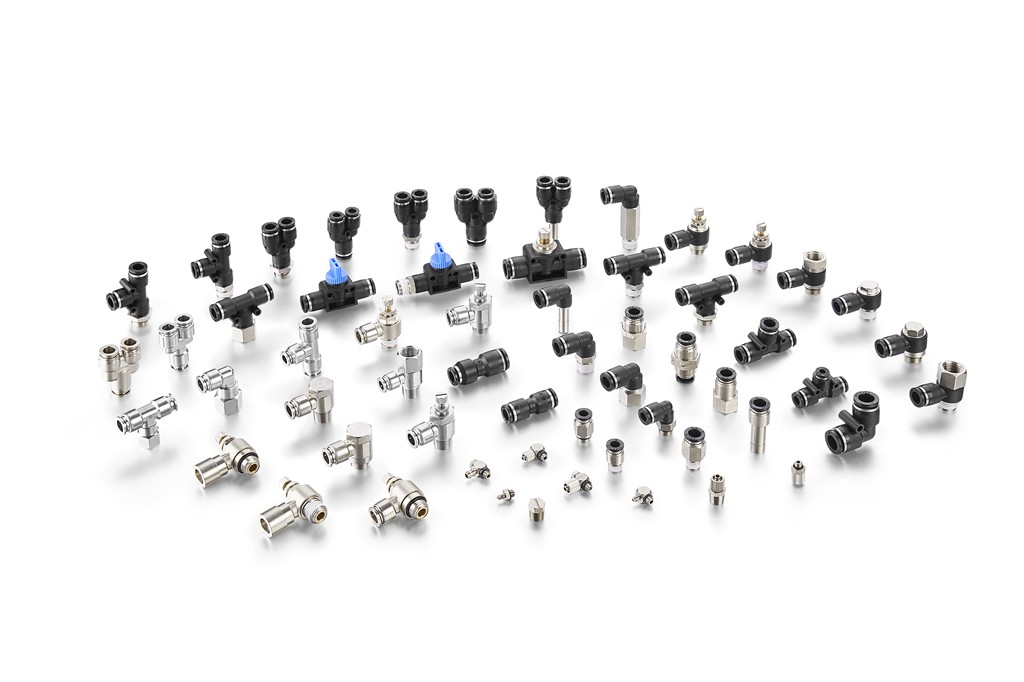
5. What Is the Difference Between Male and Female Air Fittings?
Male fittings have external threads, while female fittings have internal threads, allowing them to connect securely in pneumatic systems.
Understanding the difference between male and female air fittings is essential for selecting the right components for your system.
Fitting Type | Description | Application |
---|---|---|
Male Fittings | Have external threads or connectors, designed to fit into female fittings. | Connect to female fittings or ports, commonly used in various applications. |
Female Fittings | Feature internal threads or connectors, designed to receive male fittings. | Connect to male fittings or ports, providing a secure connection in pneumatic systems. |
6. Can Air Fittings Be Reused?
Air fittings can often be reused, but it’s important to check for wear and compatibility before reinstallation to ensure system reliability.
Factors to Consider
- Wear and Tear: Inspect for any signs of damage, such as cracks or deformation, which can compromise the fitting’s integrity. Regular inspections can help identify potential issues before they lead to failures.
- Compatibility: Ensure that the reused fitting is compatible with the existing components. Mismatched fittings can lead to leaks and system failures. Always check the specifications of the fittings to ensure they meet the requirements of your system.
- Maintenance: Regular maintenance can extend the lifespan of air fittings. Clean fittings regularly and replace any worn components to ensure optimal performance. Keeping a maintenance log can help track the condition of fittings over time.
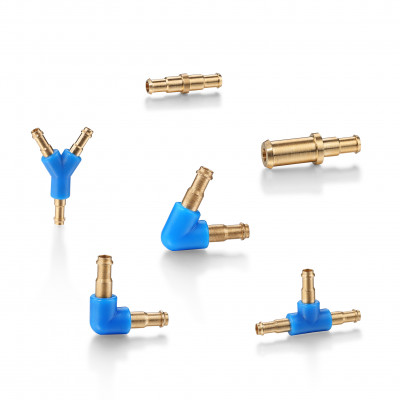
Conclusion
Selecting the right air fittings is crucial for the efficiency and safety of pneumatic systems. By understanding the different types of fittings, their mechanisms, and proper installation techniques, you can optimize your operations and prevent costly downtime. Always consider quality and compatibility when purchasing fittings, and don’t hesitate to reach out for expert advice or assistance.