I. Introduction
In the realm of industrial applications, pneumatic connections play a crucial role in the efficient operation of tools and machinery. These connections facilitate the transfer of compressed air, enabling a wide range of functions from powering pneumatic tools to controlling automated systems. Let’s delve into the world of pneumatic connections for exploring the purpose, types, components, and advantages of pneumatic connections, as well as provide practical insights into their installation and maintenance.
II. What is the Purpose of a Pneumatic Connection?
The primary purpose of a pneumatic connection is to enable the transfer of compressed air, powering tools and machinery in various applications.
Pneumatic connections serve as the backbone of pneumatic systems, allowing for the efficient transfer of compressed air. They are used in a variety of applications, such as:
- Manufacturing: Powering pneumatic tools like drills, wrenches, and conveyors.
- Automotive: Operating air brakes and pneumatic lifts.
- Construction: Facilitating the use of nail guns and air compressors.
The benefits of using pneumatic connections include increased efficiency, reduced energy consumption, and enhanced performance of pneumatic tools and machinery.
III. How Does a Pneumatic Connection Work?
Pneumatic connections work by utilizing compressed air to transmit power through a network of hoses, fittings, and valves.
At the core of pneumatic systems is the principle of compressed air. When air is compressed, it becomes pressurized and can be directed through a network of hoses and fittings. Here’s a simplified explanation of how a pneumatic connection works:
- Air Compression: An air compressor compresses ambient air, increasing its pressure.
- Air Distribution: The compressed air is directed through hoses connected to various pneumatic tools or machinery.
- Power Transmission: As the compressed air flows through the system, it powers the connected tools, enabling them to perform work.
This process allows for the efficient transfer of energy, making pneumatic systems highly effective for various applications.
IV. Types of Pneumatic Connections
Common types of pneumatic connections include push-to-connect fittings, threaded fittings, quick-disconnect couplings, and barbed fittings.
It is essential to understand the different types of pneumatic connections for selecting the right one for your application. Here are some common types:
Type | Description | Ideal Use Case |
---|---|---|
Push-to-Connect | Allows quick assembly without tools. | General applications |
Threaded Fittings | Provides a secure connection using threads. | Permanent installations |
Quick-Disconnect | Enables fast coupling and uncoupling. | Equipment maintenance |
Barbed Fittings | Uses friction to secure tubing connections. | Flexible tubing applications |
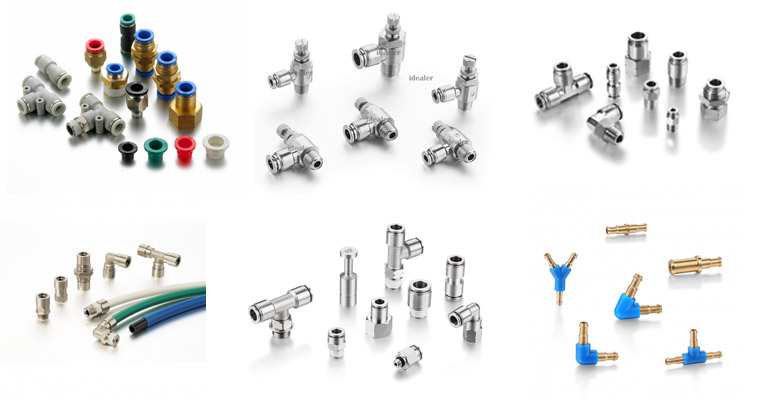
Each type has its advantages and disadvantages, and I recommend selecting the one that best fits your specific needs.
V. What Components are Involved in a Pneumatic Connection?
Key components of a pneumatic connection include fittings, hoses, valves, and compressors, all of which work together to create an efficient system.
A pneumatic connection consists of several key components that work together to ensure efficient operation:
- Fittings: Connect hoses and tools, allowing for the transfer of compressed air.
- Hoses: Transport compressed air from the compressor to the tools.
- Valves: Control the flow of air within the system, enabling precise operation.
- Compressors: Generate the compressed air needed to power the system.
Compatibility between these components is crucial for optimal performance, and I always ensure that the fittings I choose match the hoses and tools in my system.
VI. What is the Difference Between Pneumatic and Hydraulic Connections?
Pneumatic connections use compressed air, while hydraulic connections use liquids, leading to differences in pressure ratings and applications.
Here are some features for the difference between pneumatic and hydraulic connections for selecting the right system for your needs:
Feature | Pneumatic Connections | Hydraulic Connections |
---|---|---|
Fluid Type | Compressed air (gas) | Hydraulic fluid (liquid) |
Pressure Rating | Generally up to 150 psi | Often from 1,500 to over 10,000 psi |
Applications | Tools and machinery powered by air | Heavy machinery and equipment |
Material | Typically lighter materials | Durable materials for high pressure |


These differences highlight the importance of choosing the right type of connection based on the specific requirements of your application.
VII. How Do You Make a Pneumatic Connection?
Making a pneumatic connection involves assembling fittings, hoses, and tools to create a secure and efficient system.
Creating a pneumatic connection is a straightforward process. Here’s a step-by-step guide:
- Select the Right Fittings: Choose fittings that match the hoses and tools you are using.
- Cut the Hose: Ensure the hose is cut cleanly and at the correct length.
- Attach the Fitting: Insert the fitting into the hose, ensuring a snug fit.
- Connect to the Tool: Attach the other end of the fitting to the pneumatic tool or compressor.
- Test for Leaks: Once connected, turn on the air supply and check for any leaks.
By following these steps, I ensure that my pneumatic connections are secure and leak-free.
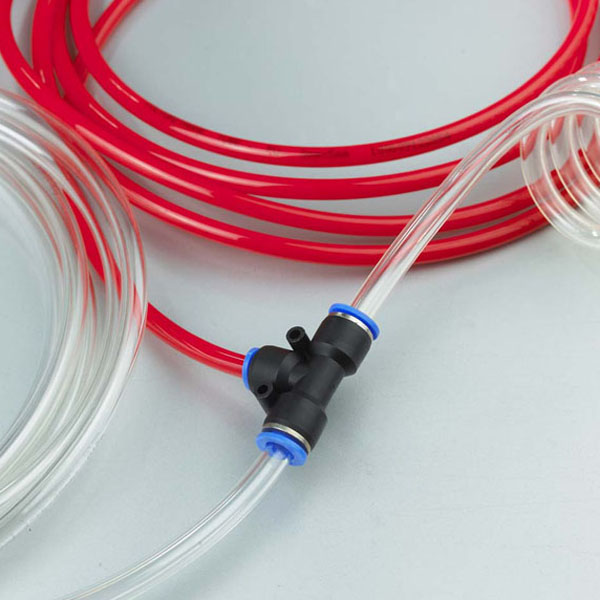
VIII. What are the Advantages of Pneumatic Connections?
Pneumatic connections offer advantages such as lightweight design, flexibility, ease of use, and cost-effectiveness.
Pneumatic connections come with several benefits that make them a popular choice in various applications:
- Lightweight: Pneumatic systems are generally lighter than hydraulic systems, making them easier to handle and install.
- Flexibility: The use of flexible hoses allows for greater maneuverability in tight spaces.
- Ease of Use: Many pneumatic fittings are designed for quick assembly and disassembly, facilitating maintenance and repairs.
- Cost-Effectiveness: Pneumatic systems often have lower initial costs compared to hydraulic systems, making them accessible for various applications.
These advantages make pneumatic connections an attractive option for many industries.

IX. What Materials are Used for Pneumatic Connections?
Common materials for pneumatic connections include plastic, brass, and stainless steel, each chosen for specific applications and environments.
The materials used in pneumatic connections play a significant role in their performance and durability. Here are some common materials:
- Plastic: Lightweight and resistant to corrosion; suitable for lower-pressure applications.
- Brass: Durable and corrosion-resistant; often used in general applications.
- Stainless Steel: Ideal for high-pressure and corrosive environments; provides excellent durability.
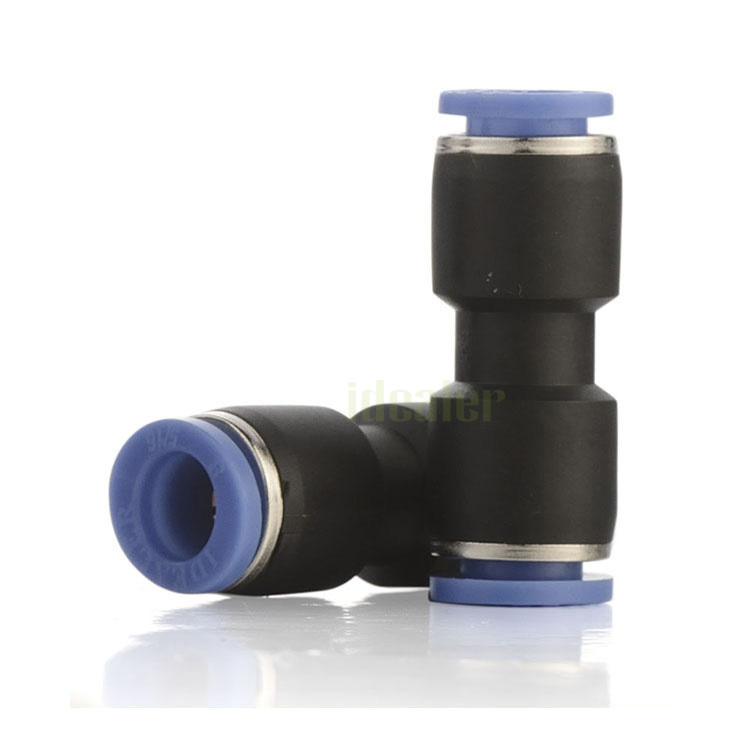

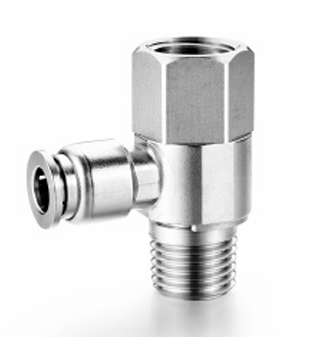
When selecting materials, I always consider the specific requirements of my application, including pressure ratings and environmental factors.
X. How Do You Troubleshoot Pneumatic Connections?
Troubleshooting pneumatic connections involves identifying common issues such as leaks and pressure drops, and applying systematic solutions.
Even with the best installations, issues can arise. Here’s how I troubleshoot pneumatic connections:
- Check for Leaks: Use soapy water to identify leaks around fittings and hoses.
- Inspect Hoses: Look for signs of wear or damage that could affect performance.
- Monitor Pressure: Use a pressure gauge to ensure the system is operating within the specified range.
- Examine Valves: Ensure that valves are functioning correctly and not obstructing airflow.
If I encounter persistent issues, I consult with a professional to ensure the system operates efficiently.
XI. What Safety Precautions Should Be Taken with Pneumatic Connections?
Safety precautions for pneumatic connections include understanding pressure ratings, using protective equipment, and conducting regular inspections.
Safety is paramount when working with pneumatic connections. Here are some precautions I always take:
- Understand Pressure Ratings: Ensure all components are rated for the maximum operating pressure to prevent failures.
- Use Personal Protective Equipment (PPE): Always wear safety goggles and gloves when working with pneumatic systems.
- Conduct Regular Inspections: I perform routine checks to identify potential issues before they become serious problems.
By prioritizing safety, I can minimize risks and ensure the reliable operation of my pneumatic systems.
XII. Conclusion
In conclusion, pneumatic connections are vital components in pneumatic systems, enabling the efficient transfer of compressed air for various applications. If you have any questions or require personalized assistance, please feel free to reach out for expert advice.