In the rapidly evolving world of energy storage, the secondary battery industry is at the forefront of innovation. As demand for high-performance, reliable batteries continues to soar, manufacturers are constantly seeking ways to enhance their production processes. One key technology that is playing a pivotal role in this transformation is pneumatic equipment.
I. How Does Pneumatic Systems Work in Every Step of Secondary Battery Productions?
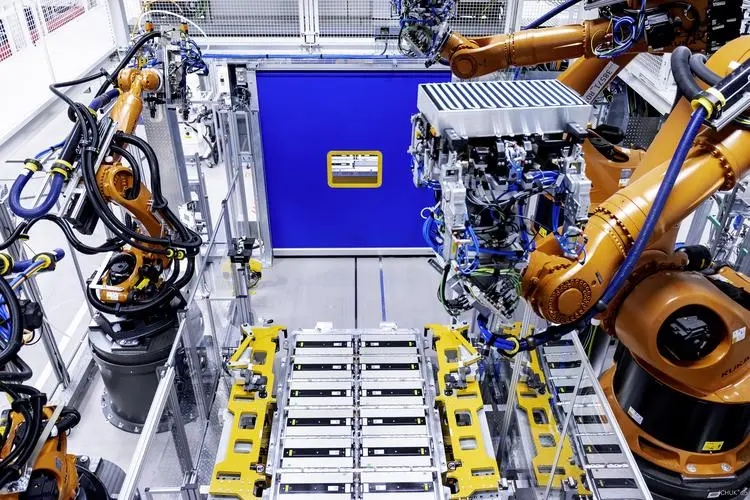
1. Electrode Production Process: Precision and Consistency
The foundation of a robust secondary battery lies in the meticulously executed electrode production process. This critical stage is where pneumatic systems truly shine, providing the precision, control, and consistency required to manufacture high-performing electrodes.
A. Mixing and Kneading
- Pneumatic agitators and mixers in the mixing and kneading machines ensure the uniform blending of electrode slurry materials.
- These pneumatic systems offer precise control over the mixing parameters, guaranteeing a homogeneous and consistent electrode mixture.
- The repeatability of the pneumatic mixing process lays the groundwork for optimal electrode performance, laying the foundation for the battery’s overall capabilities.
B. Coating and Rolling
- Pneumatic roller systems enable the precise, consistent application of electrode materials onto current collector substrates.
- The responsive, high-speed actuation of these pneumatic rollers allows for tight control over the coating thickness and uniformity.
- Precise control over the coating process is crucial in determining the battery’s energy density and cycle life, as it directly impacts the electrode’s active material loading and distribution.
C. Slitting
- Pneumatic cutting tools and die-cutters provide accurate, clean separation of electrode strips during the slitting process.
- The speed and force of these pneumatic cutters minimize material waste, ensuring efficient utilization of the electrode materials.
- High-throughput slitting enabled by pneumatic systems maximizes production output, driving efficiency and cost-effectiveness in the manufacturing process.
By leveraging the precision, repeatability, and high-speed capabilities of pneumatic technology, electrode production can be finely tuned to meet the stringent requirements of modern secondary battery design. The consistent, homogeneous mixing, precise coating, and efficient slitting facilitated by pneumatic systems lay the foundation for electrodes that deliver superior performance and reliability.
2. Cell Assembly: Tight Control and Secure Sealing
The cell assembly process is the intricate stage where the various components of a secondary battery come together to form the final product. Pneumatic technology plays a pivotal role in this critical phase, ensuring the integrity and performance of the completed cell.
A. Winding
- During the winding stage, pneumatic mandrels and tensioners ensure tight, uniform winding of the electrode layers into the cell structure.
- Precise pneumatic controls allow for accurate tension regulation throughout the winding process, resulting in consistent cell geometry and improved energy density.
- The consistent, controlled winding facilitated by pneumatic systems is essential for maximizing the battery’s power and energy capabilities.
B. Tab Attachment and Insulation
- Pneumatic placement and fastening systems accurately position and secure current collector tabs and insulating plates within the cell assembly.
- The speed and repeatability of these pneumatic automation systems enhance productivity and quality, minimizing the risk of defects during this intricate assembly step.
- Precise positioning and secure attachment of tabs and insulation plates are crucial for maintaining electrical integrity and safety within the battery cell.
C. Sealing and Electrolyte Filling
- When it comes to sealing the cell, pneumatic spot welding guns provide a secure, leak-proof enclosure of the cell lid to the case.
- Pneumatic fluid dispensers also enable controlled, consistent filling of the cell with electrolytic solution, minimizing waste and ensuring optimal electrolyte distribution.
- The pneumatic-powered sealing and filling processes safeguard the internal components of the battery, preventing potential leaks or contamination.
D. Punching, Stacking, and Tab Welding
- Punching, stacking, and tab welding processes also benefit from the integration of pneumatic technology.
- Pneumatic die-cutting presses rapidly and precisely punch electrode shapes, improving material utilization and production throughput.
- Pneumatic stackers and alignment tools accurately position and stack the electrode layers, ensuring consistent cell structure and performance.
- Pneumatic welding and lamination systems efficiently join the electrode tabs and laminate cell components, enhancing the mechanical integrity and electrical connections within the battery.
By leveraging the precision, speed, and repeatability of pneumatic systems throughout the cell assembly process, manufacturers can ensure the structural integrity, electrical performance, and safety of the final battery product. The tight control and secure sealing enabled by pneumatic technology are critical in delivering high-quality, reliable secondary batteries.
3. Inspection and Packaging: Reliable Testing and Automation
The final stages of the secondary battery manufacturing process involve rigorous inspection and packaging, where pneumatic technology once again proves its worth in ensuring the quality and integrity of the final product.
A. Electrical Testing and Aging
- Pneumatic test rigs and fixtures hold the battery cells in place during the critical electrical testing and aging processes.
- These pneumatic systems ensure consistent, repeatable positioning of the cells, enabling precise and reliable measurements of their performance characteristics.
- Accurate and repeatable testing is essential for verifying the quality and performance of the final battery product, as it allows manufacturers to identify and address any issues before the cells are packaged and shipped.
- The secure clamping and positioning provided by the pneumatic test fixtures minimize the risk of cell movement or damage during the testing procedures, further enhancing the reliability of the inspection process.
B. Packaging Automation
- In the packaging phase, pneumatic case handling, sealing, and labeling equipment automate the process, improving overall throughput and reducing the risk of damage to the delicate battery cells.
- Pneumatic case handling systems gently and precisely manipulate the battery cells, ensuring they are positioned correctly within the packaging materials.
- Pneumatic sealing mechanisms provide secure, consistent closure of the battery cases, protecting the internal components from external factors during transportation and storage.
- Pneumatic labeling and marking systems efficiently apply required identification and traceability information to the packaged batteries, streamlining the logistics and inventory management processes.
- The automated, pneumatic-powered packaging solutions enhance productivity, minimize human error, and safeguard the sensitive battery cells, ensuring they reach the end-user in pristine condition.
By integrating pneumatic technology into the inspection and packaging stages, secondary battery manufacturers can achieve a high degree of reliability, consistency, and efficiency in the final phase of the production process. This attention to detail and quality control is essential for delivering superior energy storage solutions to the market.
II. The Benefits of Pneumatic Technology in Secondary Battery Manufacturing
The integration of pneumatic equipment throughout the secondary battery production process delivers a wide range of benefits that optimize efficiency, quality, and overall throughput. These advantages make pneumatic systems an invaluable asset in the manufacturing of advanced energy storage solutions.
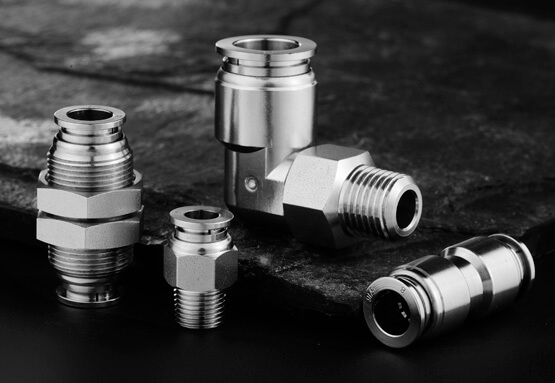
1.Precise Control and Repeatability
- Pneumatic systems offer exceptional control and repeatability, ensuring consistent product quality across the manufacturing process.
- The precise regulation of parameters such as mixing speed, coating thickness, and welding force enables tight tolerances and uniform battery cell characteristics.
- This level of precision is crucial in meeting the stringent performance and safety requirements of modern secondary batteries.
2. High-Speed Actuation and Responsiveness
- Pneumatic actuators and components provide rapid, high-speed operation, enhancing the productivity and throughput of the manufacturing lines.
- The responsive nature of pneumatic systems allows for quick, accurate movements and real-time adjustments, minimizing downtime and waste.
- This agility enables secondary battery manufacturers to keep pace with the growing demand for their products while maintaining quality standards.
3. Reliable, Durable Performance
- Pneumatic equipment is known for its robust, reliable, and durable construction, capable of withstanding the rigors of continuous, high-intensity industrial operations.
- The inherent durability of pneumatic systems ensures uninterrupted, efficient production, reducing the need for frequent maintenance or replacements.
- This dependable performance is crucial in maintaining the consistent output and cost-effectiveness of secondary battery manufacturing.
4. Flexible Integration with Automation
- Pneumatic technology integrates seamlessly with automated production systems, allowing for the development of highly integrated, efficient manufacturing lines.
- The compatibility of pneumatic equipment with advanced control systems and robotics enables the implementation of Industry 4.0 principles, driving increased productivity and data-driven optimization.
- This flexible integration enhances the overall agility and responsiveness of the secondary battery production process.
5. Clean, Oil-Free Operation
- Pneumatic systems operate using clean, oil-free compressed air, making them an ideal choice for manufacturing environments where sensitive electronic and chemical components are present.
- The absence of oil and other contaminants ensures compatibility with the delicate materials and processes involved in secondary battery production, minimizing the risk of contamination.
- This clean, environmentally friendly operation aligns with the stringent quality and safety standards of the energy storage industry.
6. Inherent Safety Features
- Pneumatic equipment is designed with robust safety features, providing a secure working environment for production personnel.
- The inherent self-contained nature of pneumatic systems, along with their ability to quickly release pressure in the event of an emergency, contributes to a safer manufacturing environment.
- This focus on worker safety is crucial in the secondary battery industry, where the handling of hazardous materials and high-energy components requires utmost precaution.
By leveraging the power and versatility of pneumatic technology, secondary battery manufacturers can optimize efficiency, quality, and throughput at every stage of the production process. From precise mixing and coating to reliable testing and automated packaging, pneumatic systems play a pivotal role in shaping the future of advanced energy storage solutions.
III. Applicable Products
In the intricate world of secondary battery production, pneumatic systems play a vital role in ensuring efficiency, precision, and reliability across the manufacturing process. These specialized pneumatic solutions comprise a range of key components that work in harmony to optimize the various stages of electrode creation, cell assembly, and final inspection and packaging.
1.Pneumatic Actuators
- Pneumatic Cylinders: These linear actuators provide the precise, repeatable motion required for tasks such as mixing, coating, punching, and stacking of battery components.
- Pneumatic Rotary Actuators: Rotary pneumatic actuators enable the controlled rotational movement needed for winding, tab welding, and other cell assembly processes.
- Air Motors: Pneumatic air motors deliver the high-speed, high-torque power required to drive mixing, kneading, and other material handling equipment.
2. Pneumatic Valves and Regulators
- Directional Control Valves: These valves precisely regulate the flow of compressed air, directing it to the appropriate pneumatic actuators and ensuring coordinated, synchronized motion.
- Pressure Regulators: Pneumatic pressure regulators maintain the optimal air pressure for each manufacturing process, ensuring consistent performance and safety.
- Flow Control Valves: By regulating the airflow, these valves enable precise control over the speed and force of pneumatic equipment, enabling fine-tuned process control.
3. Pneumatic Accessories
- Air Preparation Units: Comprehensive air preparation systems filter, regulate, and lubricate the compressed air supply, ensuring the pneumatic components operate reliably and consistently.
- Pneumatic Tubing and Fittings: High-quality tubing and fittings transfer the compressed air from the preparation units to the various pneumatic devices throughout the manufacturing facility.
- Pneumatic Sensors and Switches: These components provide feedback and monitoring of the pneumatic system’s performance, allowing for real-time adjustments and optimization.

The seamless integration of these key pneumatic components enables the creation of sophisticated, automated manufacturing systems tailored to the unique requirements of secondary battery production. From precise material handling and consistent coating to reliable cell assembly and secure packaging, the pneumatic technology powering these systems plays a pivotal role in delivering high-quality, reliable energy storage solutions.