1. Introduction
The rapid advancements in modern medicine have ushered in a new era of bio-pharmaceuticals, offering innovative therapies for complex diseases. Bio-pharmaceuticals, derived from living organisms, encompass a diverse range of products, including monoclonal antibodies, recombinant proteins, and vaccines. However, the inherent complexities of bio-pharmaceutical production demand highly specialized manufacturing processes that prioritize precision, efficiency, and regulatory compliance.
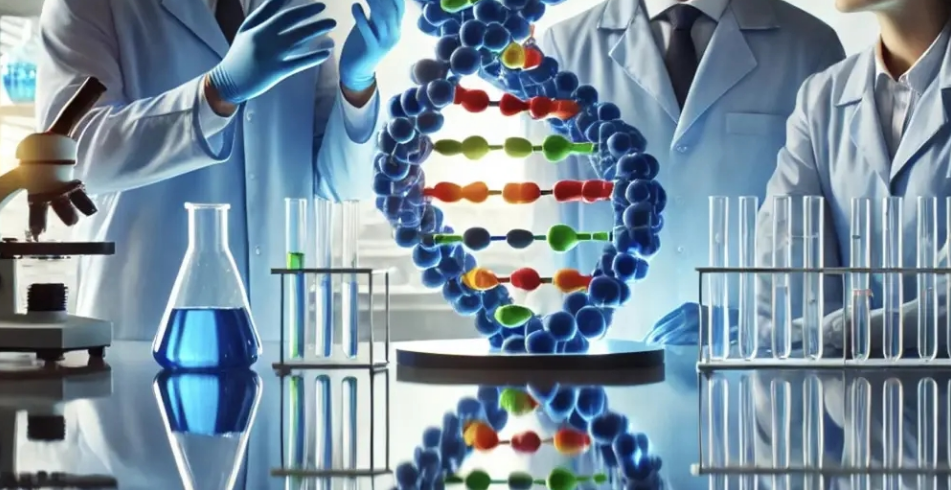
Pneumatic equipment has emerged as a transformative technology, revolutionizing the bio-pharmaceutical manufacturing landscape. Let’s delve into the role of pneumatic systems in optimizing various stages of bio-pharmaceutical production, exploring their applications, advantages, and the future trends shaping this dynamic industry.
2. Understanding Bio-Pharmaceutical Manufacturing
A. Definition of Bio-Pharmaceuticals
Bio-pharmaceuticals are medicinal products derived from living organisms, such as cells, tissues, or proteins. Unlike traditional chemically synthesized pharmaceuticals, bio-pharmaceuticals are produced through complex biological processes, necessitating meticulous management of the underlying cellular activities to convert them into effective therapeutic solutions.
This diverse range of products includes monoclonal antibodies, recombinant proteins, and vaccines, each offering unique advantages in the treatment of complex diseases, including cancer, autoimmune disorders, and genetic conditions.
B. Key Stages in the Bio-Pharmaceutical Manufacturing Process
- Cell Culture: The foundation of bio-pharmaceutical production, this stage involves cultivating living cells under carefully controlled environmental conditions to produce viable biological products. Achieving optimal growth parameters, such as nutrient supply, temperature, and oxygen levels, is crucial for maximizing cell productivity.
- Fermentation: In this phase, microorganisms are utilized to scale up the production of biological products. Precise control over fermentation conditions, including temperature, pH, and dissolved oxygen, is essential for facilitating cellular metabolism and optimizing product yields.
- Purification: Following fermentation, the target product must be isolated from cellular components, impurities, and by-products. Techniques such as filtration, chromatography, and centrifugation are employed to ensure the final bio-pharmaceutical meets stringent purity and safety standards.
- Formulation: The final stage involves preparing the bio-pharmaceutical for distribution, encompassing the mixing of active ingredients with excipients, filling into appropriate containers, and packaging. Achieving product stability, uniformity, and compliance with regulatory requirements are paramount in this phase.
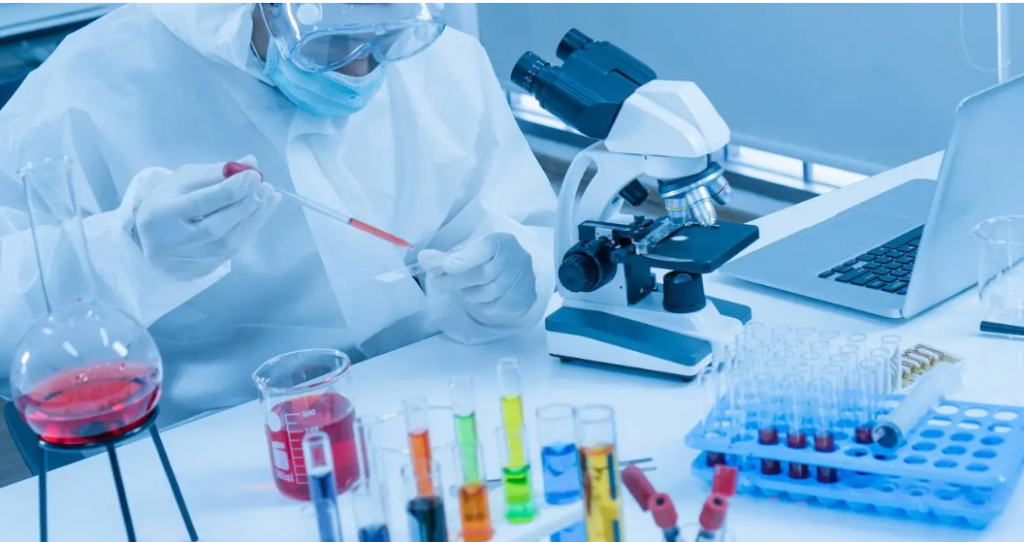
3. The Role of Pneumatic Equipment in Each Stage
A. Cell Culture and Fermentation
Pneumatic systems play a vital role in managing the critical gas delivery requirements within bioreactor systems, ensuring optimal conditions for cell growth and fermentation processes.
- Gas Delivery: Pneumatic equipment can precisely introduce and control the flow of gases, such as oxygen and carbon dioxide, into bioreactor environments. This precise gas management is essential for maintaining the appropriate dissolved oxygen levels to support cellular respiration and metabolic activities.
- Mixing and Homogeneity: Pneumatic agitation systems promote thorough mixing within bioreactors, ensuring even distribution of nutrients and fostering uniform growth conditions. This homogeneity is crucial for maximizing cell productivity and maintaining consistent product yields across production batches.
B. Material Handling
The efficient and contamination-free transfer of raw materials, intermediates, and finished products is vital in bio-pharmaceutical manufacturing. Pneumatic conveying systems excel in facilitating these material handling processes.
- Streamlined Transportation: Pneumatic conveyors can rapidly transport a wide range of materials, from powdered ingredients to liquid intermediates, directly from storage to processing areas. This speed reduces bottlenecks and enhances overall manufacturing throughput.
- Contamination Prevention: Pneumatic systems operate in closed environments, significantly minimizing the risk of external contamination. This design feature is crucial in maintaining the integrity and purity of sensitive biological products throughout the production cycle.
C. Purification Processes
Pneumatic technologies play a crucial role in optimizing the purification stage, where the target bio-pharmaceutical product is isolated from impurities.
- Efficient Filtration: Pneumatic filtration units can precisely control pressure and flow rates, enabling effective removal of unwanted cellular components and impurities while minimizing product loss.
- Centrifugation Capabilities: Pneumatic-driven centrifuges can achieve the necessary rotational speeds and processing times to facilitate the efficient separation of the desired product from cellular debris, ensuring high purity levels in the final product.
D. Formulation and Filling
The formulation and filling stages require exceptional precision to ensure product quality, safety, and regulatory compliance.
- Accurate Dosing: Pneumatic dosing systems incorporate advanced metering devices that can deliver exact quantities of active ingredients and excipients, maintaining the intended product characteristics and therapeutic efficacy.
- Automated Filling Solutions: Pneumatic filling machines operate at high speeds to fill containers, such as vials and syringes, with the formulated bio-pharmaceutical. This automation minimizes the risk of overfilling or underfilling, which could compromise product quality and compliance.
4. Advantages of Pneumatic Equipment in Bio-Pharmaceutical Manufacturing
The integration of pneumatic technology in bio-pharmaceutical manufacturing offers several key advantages that enhance operational capabilities and product quality.

A. Efficiency
Pneumatic systems are designed to facilitate rapid material transfer and continuous operation, optimizing the overall manufacturing throughput.
- Speed of Operation: Pneumatic conveyors can transport materials at significantly faster rates compared to traditional mechanical systems, reducing processing times and enabling swifter responses to market demands.
- Reduced Downtime: By minimizing bottlenecks and interruptions associated with material handling, pneumatic systems enhance overall equipment effectiveness, leading to higher production volumes.
- Continuous Operation: Many pneumatic systems can operate without interruption, ensuring a steady flow of materials through the manufacturing process. This consistency is vital for large-scale bio-pharmaceutical production, where maintaining uninterrupted supply is crucial.
B. Precision
Precision is paramount in the bio-pharmaceutical industry, as even minor variations can impact product efficacy and safety. Pneumatic equipment excels in providing the accuracy required for critical manufacturing processes.
- Accurate Dosing: Advanced pneumatic metering devices ensure that precise quantities of active ingredients and excipients are combined, maintaining the intended product formulation and therapeutic properties.
- Homogeneous Mixing: Pneumatic mixers facilitate the thorough blending of components, resulting in a consistent and uniform final product. This homogeneity is essential for ensuring the product’s safety and efficacy.
C. Flexibility
The inherent adaptability of pneumatic equipment makes it an ideal choice for versatile bio-pharmaceutical manufacturing environments.
- Seamless Integration: Pneumatic systems can be easily incorporated into existing production lines with minimal disruption, allowing manufacturers to quickly adapt to changing product requirements or regulatory standards.
- Scalability: As demand for bio-pharmaceutical products increases, pneumatic systems can be scaled up to accommodate higher production volumes without the need for extensive infrastructure modifications.
D. Cleanliness
Maintaining a clean and contamination-free environment is critical in bio-pharmaceutical manufacturing. Pneumatic systems are designed to address these stringent cleanliness requirements.
- Closed-Loop Systems: Many pneumatic conveying and processing systems operate in closed environments, significantly reducing the risk of external contamination from entering the production process.
- Minimized Manual Handling: By automating material transfers, pneumatic systems decrease the need for manual intervention, which is a common source of contamination. This automation also enhances worker safety by reducing exposure to hazardous materials.
- Ease of Cleaning: Pneumatic equipment is often engineered for easy disassembly and cleaning, enabling manufacturers to implement rigorous sanitation protocols that support compliance with Good Manufacturing Practices (GMP).
5. Future Trends in Pneumatic Technology for Bio-Pharmaceuticals
As the bio-pharmaceutical industry continues to evolve, emerging trends in pneumatic technology are poised to drive further advancements in manufacturing capabilities.
A. Increased Automation
The integration of automation in pneumatic systems will enhance operational reliability and efficiency. Smart sensors and control systems will enable real-time monitoring and dynamic adjustments, optimizing processes and reducing the risk of human error.
B. Integration of IoT Solutions
The adoption of Internet of Things (IoT) technologies will revolutionize pneumatic operations. By connecting equipment to data analytics platforms, manufacturers can gain valuable insights into performance metrics, facilitating predictive maintenance and reducing downtime.
C. Sustainability Initiatives
Future developments in pneumatic technology will likely focus on energy efficiency and environmental sustainability. Manufacturers will increasingly leverage energy-efficient pneumatic systems that consume less power while maintaining high-performance standards, contributing to the industry’s broader sustainability goals.
6. Conclusion
Pneumatic technology has emerged as a transformative force in the bio-pharmaceutical manufacturing landscape, optimizing various stages of production from cell culture to formulation. By harnessing the efficiency, precision, flexibility, and cleanliness offered by pneumatic systems, manufacturers can enhance their operational capabilities, improve product quality, and ensure compliance with stringent regulatory requirements.
As the demand for innovative bio-pharmaceutical therapies continues to grow, the strategic implementation of pneumatic equipment will be crucial for bio-pharmaceutical companies seeking to stay ahead of the curve. By embracing these advanced technologies, manufacturers can unlock new possibilities in the production of life-saving medicines, ultimately benefiting patients worldwide.
7. One of the Pneumatic Equipment-Stainless Steel Fittings
Are you looking for fittings for your machine? You can choose Stainless Steel Fittings supplier in China : Ideal-bell
A. 316L Stainless Steel One-touch Fittings(316L Stainless Steel Push-in Fittings)
- Can be used with vacuum, steam
- Working Temperature: ﹣5-150°C
- Grease-free
- Cleanliness
- Leak-free
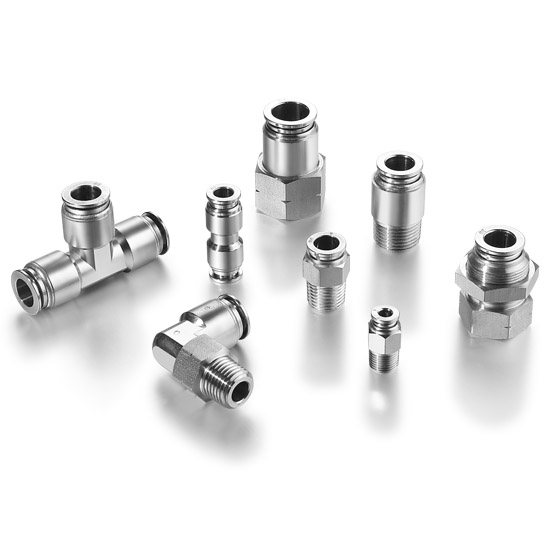
B. 316L Stainless Steel Insert Fittings(316L Stainless Steel Push-on Fittings)
- Can be used with vacuum, steam
- Working Temperature: ﹣65-260°C(No Freezing), (Swivel elbow and with sealant types:-5 -150℃)
- Grease-free
- Cleanliness
- Leak-free
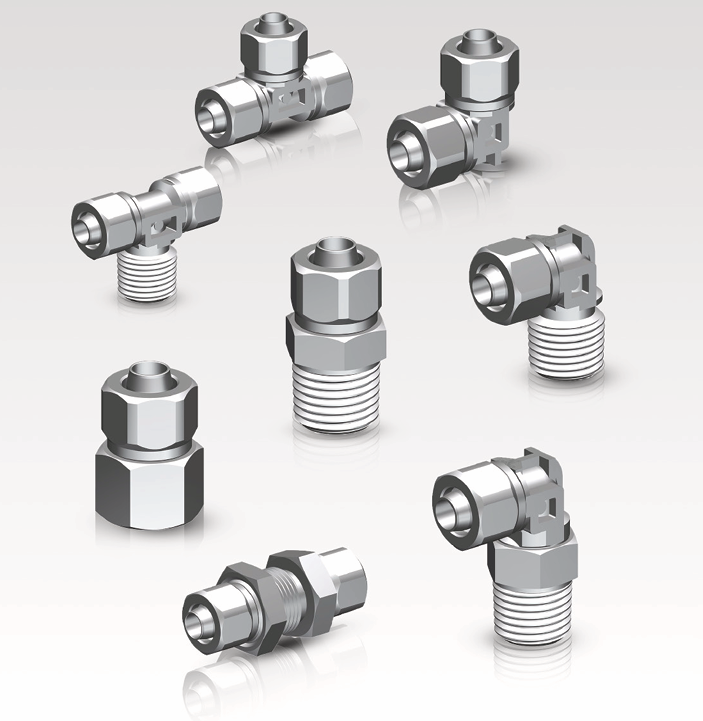
If you are looking for other pneumatic products, please contact us!